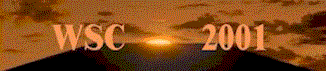 |
WSC 2001 Final Abstracts |
Future of Simulation Track
Tuesday 1:30:00 PM 3:00:00 PM
Panel: Future of Simulation
Chair: Jerry Banks (Professor Emeritus, Georgia
Tech)
Panel Session: The Future of
Simulation
Jerry Banks (Professor Emeritus, Georgia Institute of
Technology), Farhad Azadivar (University of Massachusetts Dartmouth), David
Ferrin (Accenture), John W. Fowler (Arizona State University), Daniel W.
Halpin (Purdue University), Averill M. Law (Averill M. Law & Associates),
Mani Manivannan (Vector SCM) and William S. Murphy (Defense Information
Systems Agency)
Abstract:
Panelists representing seven areas of application give
their views on the future of simulation. There is some consistency, but not a
lot. Optimization, the web, training, supply chain management, graphics, and
real time simulation received two mentions each. However, depending on how the
counting is performed, there are another six areas with a single mention.
Tuesday 3:30:00 PM 5:00:00 PM
Emulation
Chair: Ian McGregor
(Brooks Automation)
Using Emulation to Reduce Commissioning Costs on a
High Speed Bottling Line
Geoff Mueller (E2M, Inc.)
Abstract:
E˛M/Polytron builds high speed filling and packaging
systems for Fortune 100 companies. In the last year we have developed a
process to improve the quality of these systems that uses the new emulation
technology in Brooks Automation’s AutoMod simulation tool. The method, called
PolySim, enables us to functionally test control logic on a simulated 3D model
of a system prior to startup. Our first application was on a new line for
Gerber Baby Food. The project had been done without the use of the new
technology and there were some on-going controls problems with the high speed
label application area a month after startup. Using our PolySim method enabled
us to isolate and fix these controls problems in two weeks without interfering
with production. With the problem fixed, Gerber saw an 11% increase in line
efficiency.
Emulation: Debug It in the Lab – Not on the
Floor
Cindy Schiess (Design Systems, Inc.)
Abstract:
Emulation is a very powerful tool for testing and
debugging control code/logic in an office environment rather than on the plant
floor. Through the use of emulation, the actual control logic is connected to
a simulation model that imitates the actual machine/conveyance hardware. The
emulation software also has the ability to mimic the operator stations. Logic
problems can be found and corrected in the office with field time reduced to
only verifying physical, site specific, installation issues. Time, money,
aggravation, lost production, employees (from burnout), and potentially
marriages can be saved through the use of emulation.
Wednesday 8:30:00 AM 10:00:00 AM
Panel: Simulation Optimization
Chair: Justin Boesel (Mitre)
Future of Simulation Optimization
Justin
Boesel (The MITRE Corporation), Royce O. Bowden, Jr. (Mississippi State
University), Fred Glover (University of Colorado), James P. Kelly (OptTek
Systems, Inc) and Erik Westwig (Palisade Corporation)
Abstract:
The combination of simulation and optimization,
essentially unheard of in practice a decade ago, is much more accessible
today, thanks in large part to the development of commercial optimization
software designed for use with existing simulation packages. Despite this
growth, untapped applications abound. This panel, which includes developers of
simulation-optimization packages, will discuss this untapped potential,
barriers to broader applicability, and approaches for overcoming these
barriers. This paper starts off with a brief introduction by the panel's
organizer, followed by position statements from the panelists.
Wednesday 10:30:00 AM 12:00:00 PM
Data Exchange Standards for
Simulation
Chair: David Sly (EAI)
Integrating Capacity Simulation into Process
Planning
Vaughan Hetem (DaimlerChrysler)
Abstract:
Process planning in the automotive industry is referred
to as advance manufacturing engineering, because it is done in advance of
production — before the facilities are created. When developing these
processes, simulation is typically done by service groups, not the process
planner, resulting in communication errors and unnecessary iterations.
Software applications are now becoming available that not only simulate the
production throughput objective of process planning, but other planning
considerations such as process capability, material flow, ergonomics, and
interferences. The impact of these simulation tools is put into perspective
when considering the powertrain manufacturing engineering environment: process
development time in years, cycle time accuracy in seconds, cost of the
facility in hundreds of millions, and expected duration of the process in
years. That is, a single expensive opportunity to implement a long term
investment, with verification done by “simulation” experts not intimately
involved with the process. The future of simulation for me seems obvious!
Simulation Data Exchange (SDX)
Implementation and Use
Dave Sly and Shreekanth Moorthy (UGS)
Abstract:
Facility layouts of existing or proposed production
systems often form the basis of a dynamic simulation study to prove the design
concept and to determine if the required throughput (jobs per hour) can be
achieved. Traditionally, this requires the simulation engineer to duplicate
the CAD drawing in the simulation environment before being able to model it.
With sophisticated manufacturing systems such as conveyor networks, material
handling systems, automotive plants and powertrain facilities, this job can be
very difficult, time consuming and error prone. An application and interface
was needed to provide an automated integration of the layout and simulation
technologies for manufacturing. This paper discusses SDX (Simulation Data
Exchange) and its implementation.
The Expanding Role of Simulation in Future
Manufacturing
Charles McLean and Swee Leong (National Institute of
Standards and Technology)
Abstract:
Simulation technology holds tremendous promise for
reducing costs, improving quality, and shortening the time-to- market for
manufactured goods. Unfortunately, this technology still remains largely
underutilized by industry today. This paper suggests benefits to industry
resulting from the widespread, pervasive implementation of manufacturing
simulation technology. Potential simulation impact areas are closely
intertwined with strategic manufacturing. Yet, a number of factors currently
inhibit the deployment of simulation technology in industry today. The
development of new simulation interface standards could help increase the
deployment of simulation technology. Interface standards could improve the
accessibility of this technology by helping to reduce the expenses associated
with acquisition and deployment, minimize model development time and costs,
and provide new types of simulation functionality that are not available
today.
Seamless Integration of Layout and
Simulation
Karsten Mecklenburg (General Motors)
Abstract:
This document talks about the usage of Simulation Data
Exchange (SDX) (Moorthy 1999) in order to enable a consistent digital model of
automotive factories. The scope of the digital model is to plan and analyze
the factory by using different software packages. Thus the model doesn’t exist
in only one application. Therefore the consistency in terms of geometry and
process data needs to be guaranteed with external support. Whereas any
redundant information storage and rework of existing data has to be avoided.
SDX is a promising approach to accomplish this interface management.
