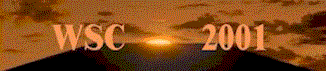 |
WSC 2001 Final Abstracts |
Manufacturing Applications Track
Monday 10:30:00 AM 12:00:00 PM
Role of Simulation in Industries
Chair: Chen Zhou (Georgia Institute of Technology)
The Definition and Potential Role of Simulation within
an Aerospace Company
Craig A. Murphy and Terrence D. Perera
(Sheffield Hallam University)
Abstract:
Simulation software has reached a technological level
that provides high flexibility and integration capabilities necessary for
product design, development and manufacturing efficiency. Within the
manufacturing industry, this simulation potential has not been fully
recognized, although it is now becoming a matter of interest through the
documented benefits it has provided. This paper discusses the issues of
simulation definition, selection and integration with both business systems
and each other. This also discusses the practical difficulties a business
would encounter in the development of a fully digital environment through
simulation integration, and data management.
Biotech Industry: Simulation and
Beyond
Prasad V. Saraph (Bayer Corporation)
Abstract:
The Biotech Industry is relatively new to the use of
simulation techniques. This paper discusses an application of discrete event
simulation in a continuous process Biotech manufacturing facility of Bayer
Corporation at Berkeley. The SIGMA® simulation model imitating demand and
supply of a critical utility (WFI - Water For Injection) was used to analyze
the WFI shortage. The model has been in use for the last year and it has
effectively eliminated WFI shortages. Based on this analysis, a set of
guidelines was designed to ensure better availability of this critical
utility. The model initiated a project to reduce the consumption of WFI. The
model was also used for strategic capacity analysis and to assess the impact
of capital projects on future budgetary plans. This whole project was
completed in two months and resulted in direct benefits worth $ 1,100,000.
A Simulation Case Study of Production Planning and
Control in Printed Wiring Board Manufacturing
Heidi M. E. Korhonen,
Jussi Heikkilä, and Jon M. Törnwall (TAI Research Centre, Helsinki University
of Technology)
Abstract:
Production planning and control in printed wiring board
(PWB) manufacturing is becoming more difficult as PWB's technology is
developing and the production routings become more complex. Simultaneously,
the strategic importance of delivery accuracy, short delivery times, and
production flexibility is increasing with the highly fluctuating demand and
short product life cycles of end products. New principles, that minimize
throughput time while guaranteeing excellent customer service and adequate
capacity utilization, are needed for production planning and control.
Simulation is needed in order to develop the new principles and test their
superiority. This paper presents an ongoing simulation project that aims at
developing the production planning and control of a PWB manufacturer. In the
project, a discrete event simulation model is built of a pilot case factory.
The model is used for comparing the effect of scheduling, queuing rules,
buffer policies, and lot sizes on customer service and cost efficiency.
Monday 1:30:00 PM 3:00:00 PM
Enterprise-wide Modeling
Chair:
Jeffrey W. Hermann (University of Maryland)
A Taxonomy of a Living Model of the
Enterprise
Larry Whitman, Kartik Ramachandran, and Vikram Ketkar
(Wichita State University)
Abstract:
A designer has a choice of many models, methods,
frameworks, and architectures. There is little consistency between these terms
among researchers. Some of the most widely used architectures and frameworks
are described with definitions and concepts that distinguish them clearly.
This paper proposes a clear definition of these terms, a clear distinction
between these and a methodology that will significantly aid in the comparison
and evaluation of various enterprise models. A direct benefit of this research
is a more clear presentation of how the enterprise modeling community uses
enterprise models.
Distributed Simulation: An Enabling Technology for
the Evaluation of Virtual Enterprises
Jayendran Venkateswaran,
Mohammed Yaseen Kalachikan Jafferali, and Young-Jun Son (The University of
Arizona)
Abstract:
This paper presents an application distributed
simulation to the evaluation of virtual enterprises. Each company or candidate
can use a simulation of its facilities to determine if it has the capability
to perform its individual function in the virtual enterprise. Then, these
simulations can be integrated into a distributed simulation of the complete
enterprise, and used to predict the viability and profitability of the
proposed product collaboration. In this paper, a prototype distributed
simulation for such a purpose is presented. First, information flows as well
as material flows among members in a virtual enterprise are identified using
IDEF? a formal function modeling method. Sequences of the identified functions
are then presented using the finite state automata formalism. These
interactions are then implemented for a commercial simulation package.
Finally, a distributed simulation composed of three individual simulations is
successfully tested across platforms over both the internet and the local area
network.
Ford's Power Train Operations – Changing the
Simulation Environment
John Ladbrook (Ford Motor Company Limited )
and Annette Januszczak (Ford Motor Company Limited)
Abstract:
This paper discusses the changes required to Ford's
Power Train Operations (PTO) simulation environment to ensure the maximum
benefit from the investment in simulation. Three key elements were identified
as essential to maximizing use. These were Availability, Support, and the
right Tools for the Job. The background driving the change was that Simulation
had been a key tool in the planning and process improvement of PTO
Manufacturing Engineering facilities since the early 80's. The original
deployment allowed users to be responsible for the selection, purchase and
maintenance of their own systems. This resulted in low utilization, high unit
cost and a diversity of products. The achievement was to transform an isolated
approach taken on two continents into a single one across 5 continents, while
significantly reducing the unit cost. The method was to select a single
software solution that could be distributed across the Ford Intranet to anyone
in PTO.
Monday 3:30:00 PM 5:00:00 PM
Simulation in Shipyards
Chair:
Young-Jun Son (University of Arizona)
Simulation of Shipbuilding
Operations
Charles McLean and Guodong Shao (National Institute of
Standards and Technology )
Abstract:
This paper discusses the objectives and requirements
for a shipbuilding simulation. It presents an overview of a generic simulation
of shipbuilding operations. The shipbuilding simulation model can be used as a
tool to analyze the schedule impact of new workload, evaluate production
scenarios, and identify resource problems. The simulation helps identify
resource constraints and conflicts between competing jobs. The simulation can
be used to show expected results of inserting new technologies or equipment
into the shipyard, particularly with respect to operating costs and schedule
impact. The use of DOD High Level Architecture (HLA) and Run Time
Infrastructure (RTI) as an integration mechanism for distributed simulation is
also discussed briefly.
Hierarchical Modeling of a Shipyard Integrated with an
External Scheduling Application
Ali S. Kiran, Tekin Cetinkaya, and
Juan Cabrera (Kiran Consulting Group)
Abstract:
This paper presents a hierarchical approach on the
simulation of large-scale discrete event systems used recently by Kiran
Consulting Group (KCG) to model shipyard operations. Because of the dynamic,
stochastic and complex nature of the shipbuilding processes, bottleneck
identification and estimation of the impact of new technology implementation
is extremely difficult to derive via analytical methods. The simulation model
of a large-scale discrete event system can be considered as a collection of
sub-systems, which are represented by the simulation models that are
independently created, modified, and saved. This approach also includes
methods that integrate these submodels into an overall model in order to run
different scenarios and identify global performance measures.
Discrete Simulation Development for a Proposed
Shipyard Steel Processing Facility
Daniel L. Williams (Electric
Boat Corporation), Daniel A. Finke (The Pennsylvannia State University), D. J.
Medeiros (Department of Industrial & Manufacturing Engineering) and Mark
T. Traband (Applied Research Laboratories)
Abstract:
This paper describes the efforts required to convert
conceptual designs and undefined processes for a proposed advanced steel
processing shipyard facility into a discrete event simulation. Modeling of a
completely non-existent entity poses many difficulties, yet the results can
still be beneficial. The lack of actual production data and corresponding
business rules, causes an in-depth review of all available information
combined with that which can be extrapolated from vendor specification sheets
or human experience. Most of the equipment required for this advanced
processing facility will be custom built to suit the needs of this highly
technical complex. This facility which will ultimately support construction of
vessels, was driven by high expectations of improved production efficiencies.
The model is expected to support not only the pre-construction design phases
of the building, but also to serve as a post-construction production planning
tool.
Tuesday 8:30:00 AM 10:00:00 AM
Process Control and Improvement
Chair: Farhad Azadivar (University of Massachusetts Dartmouth)
Prediction of Process Parameters for Intelligent Control
of Freezing Tunnels Using Simulation
Sreeram Ramakrishnan, Richard
A. Wysk, and Vittaldas V. Prabhu (Pennsylvania State University)
Abstract:
Various analytical and empirical methods assuming the
existence of steady state and requiring homogenous properties of the product
have been used with limited success in estimating freezing times in the food
processing industry. Irrespective of the method adopted for estimating
freezing time requirements, a critical process issue that needs to be
considered is that of system control. Simulation models suggest that a
feed-forward control strategy, as discussed in this paper, can be used to
control a freezing tunnel and obtain considerable energy savings while
ensuring ‘appropriate’ freezing of all products. The control strategy
discussed in this paper, involves the continuous monitoring of product input
and controlling either or both of the refrigerant flow and conveyor speed. The
primary objective of this paper is to demonstrate the use of simulation to
predict process parameters for ‘intelligent control’ of freezing tunnels, and
provide an estimate of potential energy savings.
Quantifying Simulation Output Variability Using
Confidence Intervals and Statistical Process Control
Amy Jo Naylor
(Corning Inc.)
Abstract:
Two types of variability can occur in model output:
variability between replications and variability within each replication. The
objective of the model combined with the type of output variability determines
which tool is more appropriate for output analysis. Many output analysis
techniques are used to translate simulation model results into a format that
answers the model objective. This paper compares two tools for output
analysis: confidence intervals and statistical process control. Each tool
quantifies a different type of variaiton from the model results. As such,
statistical process control is applied beyond monitoring the consistency of
run data. A supply chain example with one factory, multiple parts, and
multiple distribution centers is used throughout the paper to illustrate these
concepts.
Plate/Sheet Nest Release and Throughput Simulation for
WSC ’01
Leland D. Weed (The Raymond Corporation)
Abstract:
The BT/Raymond Corporation is a manufacturer of narrow
aisle electric fork-trucks and uses two Delmia simulation software packages:
UltraArc® and Quest®. In the Greene NY facility, one of the Quest® simulations
shows the start of the fabrication process. The plate/sheet line is a group of
machines that punch, machine, profile, and form steel material ranging in
thickness from 0.030” to 1.250”. Since each product is built to customer
order, the mix of parts to produce on the line is continually changing. The
simulation of this process reads the data that schedules the work for the
various machines, then runs the line showing capacity and throughput issues a
day ahead of the factory floor run. The data that the model reads can also be
changed to experiment with different product build quantities.
Tuesday 10:30:00 AM 12:00:00 PM
Decision Making using Simulation
Chair: Durk-Jouke van der Zee (University of
Groningen)
Solving Sequential Decision-Making Problems Under
Virtual Reality Simulation System
Yang Xianglong, Feng Yuncheng,
and Li Tao (Beijing University of Aeronautics & Astronautics) and Wang Fei
(Institute of International Economy,State Development Planning Commission of
China)
Abstract:
A large class of problems of sequential decision-making
can be modeled as Markov or Semi-Markov Decision Problems, which can be solved
by classical methods of dynamic programming. However, the computational
complexity of the classical MDP algorithms, such as value iteration and policy
iteration, is prohibitive and will grow intractably with the size of problems.
Furthermore, they require for each action the one step transition probability
and reward matrices, which is often unrealistic to obtain for large and
complex systems. Here, we provide the decision-maker a sequential
decision-making enviroment by establishing a virtual reality simulation
system, where the uncertainty property of system can also be shown. In order
to obtain the optimal or near optimal policy of sequential decision problem,
simulation optimization algorithms as infinitesimal perturbation analysis are
applied to complex queuing systems. We present a detailed study of this method
on the sequential decision-making problem in Boeing-737 assembling process.
Modelling and Improving Human Decision Making with
Simulation
Stewart Robinson, Thanos Alifantis, and Robert Hurrion
(Warwick Business School), John Edwards (Aston Business School), John Ladbrook
(Ford Motor Company) and Tony Waller (Lanner Group)
Abstract:
Modelling human interaction and decision-making within
a simulation presents a particular challenge. This paper describes a
methodology that is being developed known as 'knowledge based improvement'.
The purpose of this methodology is to elicit decision-making strategies via a
simulation model and to represent them using artificial intelligence
techniques. Further to this, having identified an individual's decision-making
strategy, the methodology aims to look for improvements in decision-making.
The methodology is being tested on unplanned maintenance operations at a Ford
engine assembly plant.
Tuesday 1:30:00 PM 3:00:00 PM
Manufacturing Controls
Chair:
Amarnath Banerjee (Texas A&M University)
Understanding the Fundamentals of Kanban and CONWIP
Pull Systems Using Simulation
Richard P. Marek (Ford Motor
Company), Debra A. Elkins (General Motors) and Donald R. Smith (Texas A&M
University)
Abstract:
This paper presents an introductory overview and
tutorial in simulation modeling and control of serial Kanban and CONWIP
(CONstant Work In Process) pull systems using ARENA/SIMAN 3.5/4.0. Card level
estimation is discussed for both types of pull systems, and a heuristic method
to adjust card levels controlling system WIP (Work In Process) is provided.
The objective is to present a tutorial for students and practicing engineers
familiar with the basics of simulation, but unfamiliar with pull system
fundamentals.
Real-Time Adaptive Control of Multi-Product
Multi-Server Bulk Service Processes
Durk-Jouke van der Zee
(University of Groningen)
Abstract:
Batching jobs in a manufacturing system is a very
common policy in most industries. Main reasons for batching are avoidance of
setups and/or facilitation of material handling. Batch processing systems
often consist of multiple machines of different types for the range and
volumes of products that have to be handled. Building on earlier research in
aircraft industry, where the process of hardening synthetic aircraft parts was
studied, we discuss a new heuristic for the dynamic scheduling of these types
of systems. It is shown by an extensive series of simulation experiments that
the new heuristic outperforms existing heuristics for most system
configurations.
Improving Simulation Model Adaptability with a
Production Control Framework
Sean M. Gahagan and Jeffrey W.
Herrmann (Institute for Systems Research)
Abstract:
Simulation models provide a powerful tool for the
analysis of manufacturing systems, but their utility beyond the design stage
of the system life cycle is hampered by the high cost of model maintenance. To
reduce this cost, models must be made more adaptable. We believe that
adaptability can be increased by separating the flow of material from the flow
of information through a model system, especially with respect to changes
related to production control. Coordination of these flows, however, requires
a production control framework. In this paper, we propose a three-level,
hierarchical production control framework and define the elements necessary to
implement it in a simulation model. We demonstrate the use of this approach by
considering a simple flow shop undergoing production control changes. We
define the parameters of the shop using the framework and implement the
changes with little effort.
Tuesday 3:30:00 PM 5:00:00 PM
Analysis of Manufacturing Systems
Chair: Chen Zhou (Georgia Institute of Technology)
Computer Simulation Analysis of Electricity Rationing
Effects on Steel Mill Rolling Operations
Thomas F. Brady (Purdue
University North Central)
Abstract:
This paper presents an application of computer
simulation as a policy analysis tool for the electric utility industry. In the
last decade, the amount of electricity generation capacity has remained
constant while demand for electricity has been increasing. This situation puts
industrial electricity users, those who use large highly varying quantities of
electricity in potentially risky production and financial situations. In this
paper, we describe a computer simulation model that examines the electricity
requirements of a steel mill in a constrained electricity supply environment.
By using simulation, we develop and analyze policies that quantify the costs
and benefits of collaborative strategies for efficient electricity usage from
both perspectives.
A Practical Bottleneck Detection
Method
Christoph Roser, Masaru Nakano, and Minoru Tanaka (Toyota
Central Research and Development Laboratories)
Abstract:
This paper describes a novel method for detecting the
bottleneck in a discrete event system by examining the average duration of a
machine being active for all machines. The machine with the longest average
uninterrupted active period is considered the bottleneck. The method is widely
applicable and also capable of analyzing complex and sophisticated systems.
The results are highly accurate, distinguishing between bottleneck machines
and non-bottleneck machines with a high level of confidence. This approach is
very easy to use and can be implemented into existing simulation tools with
little effort, requiring only an analysis of the log file which is readily
available by almost all simulation tools. This method satisfies not only
academic requirements with respect to accuracy but also industry requirements
with respect to usability.
Using Simulation and Neural Networks to Develop a
Scheduling Advisor
Thanos Alifantis and Stewart Robinson
(University of Warwick)
Abstract:
The research using artificial intelligence and computer
simulation introduces a new approach for solving the job shop scheduling
problem. The new approach is based on the development of a neural
network-scheduling advisor, which is trained using optimal scheduling
decisions. The data set, which is used to train the neural network, is
obtained from simulation experiments with small-scale job shop scheduling
problems. The paper formulates the problem and after a review of the current
solution methods it describes the steps of a new methodology for developing
the neural network-scheduling advisor and collecting the data required for its
training. The paper concludes by mentioning the expected findings that can be
used to evaluate the degree of success of the new methodology.
Wednesday 8:30:00 AM 10:00:00 AM
Automation in Modeling
Chair:
Chen Zhou (Georgia Institute of Technology)
Using Automation for Finishing Room Capacity
Planning
Ryan Heath Melton (CMD Systems) and C. Thomas Culbreth,
Stephen D. Roberts, and Jeffrey A. Joines (North Carolina State University)
Abstract:
Capacity planning of a furniture finishing system using
both deterministic analysis and stochastic simulation is conveniently
performed with the aid of ActiveX Automation Users interactively build a
complete model of a finishing system with an Excel interface, which creates a
deterministic model. The spreadsheet decouples data input from the simulation
model construction and execution, and provides a user-friendly tool for
analyzing a finishing system. Using the spreadsheet, simulation data is
provided to the deterministic model, and an Arena simulation model and
animation of individual finishing line operations is constructed through
ActiveX automation. A manufacturing manager unfamiliar with modeling
techniques can use the interface to plan the finishing system and conduct
simulation experiments with various input parameters such as line loading
techniques, operations balancing, and line speeds. Through the interface,
results from the simulation can be used in an iterative process to analyze and
refine design parameters of the finishing line.
Computer-Aided Manufacturing Simulation (CAMS)
Generation for Interactive Analysis – Concepts, Techniques, and
Issues
Boonserm Kulvatunyou and Richard A. Wysk (Pennsylvania State
University)
Abstract:
Simulation model is usually developed as a one-time use
analytical model by a system analyst (usually from external firm) rather than
for a routine and interactive use by a shop floor engineer. This is because it
usually takes longer time to generate a result from the simulation, and the
simulation model of manufacturing system is usually too sophisticated and time
consuming to use as an interactive tool by the manufacturing/production
engineer. A CAMS reduces this complication by encapsulating the
‘complicated-logic’ and automating the ‘tedious data-acquisition’ with a more
user-friendly interface like a spreadsheet or database input form. This paper
describes how CAMS can automatically generate a simulation model;
specifically, techniques and issues to structure the model to hide those
tasks, so that it is a user-friendly interactive decision support with minimal
amount of automation code. The paper concludes with a capacity analysis
example from the real industry.
Database Driven Factory Simulation: A
Proof-of-Concept Demonstrator
Lars G. Randell and Gunnar S. Bolmsjö
(Lund University)
Abstract:
The paper presents a database-based method to reduce
the development time and project lead-time for large discrete-event simulation
models of entire factories. The database used to automatically generate and
drive the simulation model is a copy of the production planning database. A
set of proof-of-concept tools and a database have been generated to verify the
method and it has been shown that it is feasible to run a simulation using the
production planning data as the only information source. The software
developed is modular and designed to work in heterogeneous environments. The
method is expected to reduce the modeling and maintenance effort considerably
when modeling entire factories. The method will result in a holistic and
fairly accurate assessment of performance measures for an entire factory.
Wednesday 10:30:00 AM 12:00:00 PM
General Manufacturing
Applications
Chair: Larry E. Whitman (Wichita State University)
Feasibility for Automatic Data
Collection
Neil H. Robertson and Terrence Perera (Sheffield Hallam
University)
Abstract:
It is argued that the data collection process is the
most crucial and time consuming stage in the model building process. This is
primarily due to the influence that data has in providing accurate simulation
results. Data collection is an extremely time consuming process predominantly
because the task is manually orientated. Hence, automating this process of
data collection would be extremely advantageous. This paper presents how
simulation tools could utilize the Corporate Business Systems as the potential
source for simulation data. Subsequently a unique interface could be developed
and implemented to provide this data directly to the simulation tool. Such an
interface would prove to be an invaluable tool for users of simulation.
A Virtual Environment for Simulating Manufacturing
Operations in 3D
Ravi Chawla and Amarnath Banerjee (Texas A&M
University)
Abstract:
This paper presents a method for simulating basic
manufacturing operations (unload, load, process, move, and store) in a 3D
virtual environment. The virtual environment provides a framework for
representing a facility layout in 3D, which encapsulates the static and the
dynamic behavior of the manufacturing system. The 3D manufacturing objects in
the facility are mapped with the nodes in the framework. The framework, a
modified scenegraph structure, is a tree structure, which can be manipulated
by updating the parent-child relationships and the transformation matrix to
simulate the basic manufacturing operations. The method can be easily extended
to represent more specific manufacturing operations.
