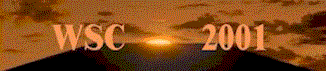 |
WSC 2001 Final Abstracts |
Semiconductor Manufacturing Track
Monday 10:30:00 AM 12:00:00 PM
Bottleneck Equipment Management
Chair: Oliver Rose (University of Würzburg)
Simulating Test Program Methods in Semiconductor
Assembly Test Factories
Chad D. DeJong (Intel Corporation)
Abstract:
Significant opportunities for improvement in
semiconductor manufacturing reside in the Test areas. These Test areas can
often be the system constraint, due to complex testing policies, bin-to-order
mapping, and cost. A very difficult problem is to determine the best methods
for assigning test programs for lots on these test equipment. To answer these
problems, Intel has produced dynamic discrete event simulation models that
consider multiple wafer types, multiple end products, multiple test program
methods, and binning policies of end products according to the tested
performance of the die. This model does not require modeling specific
manufacturing equipment and operator activities, only detailed logic of test
program and binning policies. The quantitative output data from this model
provides the relative decision support necessary to determine what methods
work best for Intel, given other costs and business drivers.
How “Overstaffing” at Bottleneck Machines Can
Unleash Extra Capacity
Robert C. Kotcher (Headway Technologies,
Inc.)
Abstract:
Using simulation, Headway Technologies predicted that
increasing staffing among a group of already lightly loaded machine
operators-—"overstaffing"—-would significantly improve throughput of its
factory. This was counterintuitive since the operators already had significant
idle time. Yet time studies confirmed that bottleneck equipment for which
these operators were responsible was spending over 22% of its uptime idle
solely due to lack of an operator. Analysis showed how this could be so:
production equipment has a frequent and unpredictable need for operators, yet
the operators must spend time away from the equipment tending to other demands
of their jobs. A method of estimating the cost of this operator-induced
throughput loss is described. The result shows how extremely profitable the
hiring of extra operators is in such situations. A means of estimating the
most profitable level of staffing is also described, along with several
alternative solutions for reducing operator absences.
Simulation-Based Solution of Load-Balancing Problems in
the Photolithography Area of a Semiconductor Wafer Fabrication
Facility
Lars Mönch (Technical University of Ilmenau) and Matthias
Prause and Volker Schmalfuss (X-FAB Semiconductor Foundries AG)
Abstract:
In this paper we present the results of a simulation
study for the solution of load-balancing problems in a semiconductor wafer
fabrication facility. In the bottleneck area of photolithography the steppers
form several different subgroups. These subgroups differ, for example, in the
size of the masks that have to be used for processing lots on the steppers of
a single group. During lot release it is necessary to distribute the lots over
the different stepper groups in such a way that global targets like cycle time
minimization, the maximization of the number of finished lots and due date
performance are inside a certain range. We present a simulation model of a
wafer fab that models the photolithography area in a detailed manner. By means
of this simulation model it is possible to decide at release time on which
stepper subgroup processing of the lots of a certain product is favorable.
Monday 1:30:00 PM 3:00:00 PM
Cycle Time versus Throughput Analysis
Chair: DeJong Chad (Intel)
An Overall Framework for Generating Simulation-Based
Cycle Time-Throughput Curves
Sungmin Park (Korea Gas Corporation)
and Gerald T. Mackulak and John W. Fowler (Arizona State University)
Abstract:
A simulation-based cycle time-throughput curve requires
a large amount of simulation output data, and an experimentation framework is
needed to enhance the precision and accuracy of a simulation-based cycle
time-throughput curve. In this research, approaches and solutions are
presented on three prime issues: 1) the establishment of the simulation
sampling strategies; 2) the determination of the simulation sequences; and 3)
the determination of the length of a simulation run. First, strategic
simulation sampling guidelines are proposed as to how to use a fixed amount of
samples when trying to generate a precise and accurate cycle time-throughput
curve for complex systems. Second, in order to provide good references for the
sequential experiments to generate precise simulation-based cycle
time-throughput curves, a set of discrete design points is ranked
sequentially. Third, a sequential stopping rule is developed to determine the
length of a simulation run based on a time series forecasting procedure.
Sizing a Pilot Production Line Using
Simulation
Peng Qu, Geoffrey E. Skinner, and Scott J. Mason
(University of Arkansas)
Abstract:
The semiconductor industry is rapidly expanding
worldwide. With the continuing advancement of technology, companies are
continually striving to develop and maintain cutting edge products to stay
“ahead of the curve.” As a result, old and new companies alike often have the
need to develop pilot production lines to test new engineering and processing
ideas. We present a case study example of how simulation can be used to
establish the initial tooling and operator requirements for pilot production
lines, as well as to estimate the fixed and recurring costs associated with
the line.
Critical Tools Identification and Characteristics
Curves Construction in a Wafer Fabrication Facility
Dima Nazzal and
Mansooreh Mollaghasemi (University of Central Florida)
Abstract:
The purpose of this research was to identify the
factors in a wafer fabrication facility that significantly affect the cycle
times of two main technologies that are currently in process and in demand for
the next few years. Moreover, the goal was to construct the characteristics
curves that would provide information about the different capabilities of a
wafer fabrication facility for several improvement scenarios. A valid
simulation model of the whole production line of the fabrication facility was
built. The input factors in the fab that significantly affect cycle time, were
identified through factor screening experiments. Based on these factors,
several scenarios involving addition of tools, were identified and the
characteristics curves were constructed for each scenario. These
characteristics curves were used to relate cycle time to production volume
capacities.
Monday 3:30:00 PM 5:00:00 PM
Scheduling and Dispatching
Chair:
Russell Barton (Penn State University)
Scheduling Batch Processing Machines in Complex Job
Shops
Kasin Oey and Scott J. Mason (University of Arkansas)
Abstract:
This paper considers a complex job shop problem with
reentrant flow and batch processing machines. A modified shifting bottleneck
heuristic (MSB) is considered for generating machine schedules to minimize the
total weighted tardiness. We observe that the MSB could produce infeasible
schedules where cyclic schedules are found. A cycle elimination procedure is
proposed to remove the possibility of the MSB generating cyclic schedules in
the solution.
Scheduling Setup Changes at Bottleneck Facilities in
Semiconductor Manufacturing
Zaid Duwayri (i2 Technologies) and
Mansooreh Mollaghasemi and Dima Nazzal (University of Central Florida)
Abstract:
In this paper, a scheduling heuristic was developed to
aid the operators in semiconductor fabs in choosing what type of lots to
process next on bottleneck facilities, and whether to change machine setup in
order to reduce cycle time. The scheduling heuristic aims at balancing
workload levels for implanters processing lots at different stages of the
wafer production lifecycle. This is accomplished by processing lots that
contribute most to increasing inventory levels at the bottleneck facility. A
whole production line simulation model was used to evaluate the performance of
the scheduling heuristic and to compare it against several commonly used
scheduling heuristics with respect to mean cycle time, work in process (WIP),
and standard deviation of cycle time. Simulation results showed that the
heuristic performed better than all other rules in terms of mean cycle time
and WIP in all cases, and better in terms of standard deviation of cycle time
for most cases tested.
Dispatching Heuristic for Wafer
Fabrication
Loo Hay Lee, Loon Ching Tang, and Soon Chee Chan
(National University of Singapore)
Abstract:
As the semiconductor industry moves into the next
millennium, companies increasingly will be faced with production obstacles
that impede their ability to remain competitive. Effective equipment and line
management planning will increasingly be required to maximize profitability
while maintaining the flexibility to keep pace with rapidly changing
manufacturing environment. In this paper, the authors present a two-bottleneck
machines center model for wafer operations analysis. A new dispatching rule
Balance Work Content, BWC, is introduced. This is a selective dispatching rule
whereby it attempts to maximize the utilization of bottleneck machine. A
systematic approach to assessing the impact of BWC is presented. Extensive
simulation runs on both the deterministic and stochastic models developed
shows its supremacy over conventional approaches of FIFO and SPT.
Tuesday 8:30:00 AM 10:00:00 AM
Modeling Methodology
Chair:
Scott Mason (University of Arkansas)
The Shortest Processing Time First (SPTF) Dispatch Rule
and Some Variants in Semiconductor Manufacturing
Oliver Rose
(University of Würzburg)
Abstract:
Looking for appropriate dispatch rules for
semiconductor fabrication facilities (wafer fabs), practitioners often intend
to use the Shortest Processing Time First (SPTF) rule because it is said to
reduce cycle times. In our study, we show, however, that this positive effect
on cycle times can be achieved in single machine systems but not necessarily
in complete wafer fabs. In addition, we discuss variants of the SPTF rule.
Implementation of Response Surface Methodology Using
Variance Reduction Techniques in Semiconductor
Manufacturing
Charles D. McAllister, Bertan Altuntas, and Matthew
Frank (The Pennsylvania State University) and Juergen Potoradi (Infineon
Technologies)
Abstract:
Semiconductor manufacturing is generally considered a
cyclic industry. As such, individual producers able to react quickly and
appropriately to market conditions will have a competitive advantage.
Manufacturers who maintain low work in process inventory, ensure that
specialized equipment is in good repair, and produce quality products at least
possible cost will have the best opportunities to effectively compete and
excel in these challenging venues. To support this nimble business model, our
current efforts are directed toward creating efficient, accurate metamodels of
the impact of maintenance policies on production efficiency. These validated
polynomial approximations facilitate rapid exploration of the design region,
compared with the original simulation models. The experiment design used for
metamodel construction employed variance reduction techniques. When compared
to a similar experiment design using independent streams, the variance
reduction approach provided a decrease in standard error of the regression
coefficients and smaller average error when validated against the simulation
response.
Graphical Methods for Robust Design of a Semiconductor
Burn-In Process
Scott L. Rosen, Chad A. Geist, Daniel A. Finke,
Jyotirmaya Nanda, and Russell R. Barton (The Pennsylvania State University)
Abstract:
Discrete-event simulation is a common tool for the
analysis of semiconductor manufacturing systems. With the aid of a simulation
model, and in conjunction with sensitivity analysis and metamodeling
techniques, robust design can be performed to optimize a system. Robust design
problems often include integer decision variables. This paper shows a
graphical approach to robust design that is effective in the presence of
discrete or qualitative variables. The graphical robust design methodology was
applied to a backend semiconductor manufacturing process. Changes in specific
resource capacities and product mix were examined to determine their effect on
the level and variance of cycle time and work in process.
