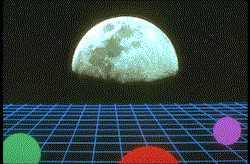 |
WSC 2002 Final Abstracts |
Manufacturing Applications Track
Monday 10:30:00 AM 12:00:00 PM
Manufacturing 1
Chair: Deb
Medeiros (The Pennsylvania State University)
Simulation-Based Analysis of a Complex Printed Circuit
Board Testing Process
Jeffrey S. Smith and Yali Li (Auburn
University) and Jason Gjesvold (Soldering Technology International, Inc.)
Abstract:
This paper describes a simulation-based analysis of a
printed circuit board (PCB) testing process. The PCBs are used in a defense
application and the testing process is fairly complex. Boards are mounted on a
test unit in batches and go through three thermal test cycles. As boards fail
testing during the thermal cycling, operators can either replace the failed
boards at fixed points during the cycling or can allow the test unit to
complete the testing cycle before removing failed boards. The primary
objective of the simulation study is to select an operating strategy for a
given set of operating parameters. A secondary objective is to identify the
operating factors to which the strategy selection is sensitive. Initial
testing indicated that failed boards should be replaced as soon as possible
under the current operating configuration of the sponsor’s facility. Secondary
testing is also described.
A Simulation Study of High Power Detonator
Production Transition
Johnell Gonzales-Lujan and Robert J. Burnside
(Los Alamos National Laboratory) and George H. Tompkins (Los Alamos)
Abstract:
Due to changes in production requirements the current
facility was no longer adequate. A simulation study was conducted to help
quantify the impacts of additional capacity, when that capacity should be
brought online, and how to manage production in the interim before the new
facility is available.
Capacity Analysis of Multi-Product, Multi-Resource
Biotech Facility Using Discrete Event Simulation
Prasad V. Saraph
(Biological Products, Bayer Healthcare)
Abstract:
Use of simulation for capacity analysis is an upcoming
field in Biotech industry. This paper discusses an application of discrete
event simulation in the multi-product and multi-resource Filling Freeze-Drying
facility of Bayer Corporation’s Berkeley site. The SIGMA® simulation model was
used to estimate the current and future throughput capacity by taking into
account current operations and various capital and efficiency improvement
projects planned for near future. The model also identified certain project
clusters with potential for large capacity gains, which otherwise would not
have been visible. The model and its outcome are in use since 2001.
Monday 1:30:00 PM 3:00:00 PM
Manufacturing 2
Chair: Todd
Lebaron (Brooks Automation)
Shop Scheduling Using Tabu Search and
Simulation
Daniel A. Finke, D. J. Medeiros, and Mark T. Traband
(The Pennsylvania State University)
Abstract:
An important goal in scheduling products through a
manufacturing facility is to assure that the work is completed as close as
possible to its due date. Work that is late creates downstream delays, while
early completion can be detrimental if storage space is limited. This paper
reports initial results in developing a scheduling procedure for an automated
steel plate fabrication facility. The approach uses Tabu search combined with
simulation to schedule product through a set of machines. Performance of the
procedure is evaluated by comparison to the optimal solution for small problem
instances, and to a good heuristic for larger problems. Results show that the
Tabu search method works well for this problem. Combining Tabu search with
simulation allows the incorporation of more realistic constraints on system
operation.
A Simulation Study of Robotic Welding System with
Parallel and Serial Processes in the Metal Fabrication
Industry
Carl R. Williams and Peraset Chompuming (University of
Memphis)
Abstract:
This paper presents the usefulness of simulation in
studying the impacts of system failures and delays on the output and cycle
time of finished weldments produced by a robotic work cell having both serial
and parallel processes. Due to multiple processes and overlapped activities,
process mapping plays a significant role in building the model. The model
replicates a non-terminating welding fabrication system with duplicate
stochastic events caused by system failures and delays. A full factorial model
is employed and analyzed to examine the main and interaction effects of five
major types of system failures and delays via multiple regression analysis.
The analysis derived from the full factorial model shows that material
handling carrier delays have the most significant impact on the cycle time.
This case study illustrates a modeling approach with system verification and
validation revealing fundamental system design flaws which cause a significant
loss of production.
Creation of a Self Adaptive Simulation for Radex
Heraklit Industries
Shabnam Tauböck, Christian Wartha, and Michael
Steiner (ARC Seibersdorf Research), Gerhard Pirkner (Didier-Werke AG, Werk
Marktredwitz) and Felix Breitenecker (Vienna University of Technology)
Abstract:
The main goal of this project was to create a
simulation of the production plant of Radex Heraklit Industries (RHI) that
offers the possibility to change the structure of the model by adding machines
and furnaces and change system parameters. The large amount of data needed
soon implied the use of a database connected to the simulation. This resulted
in a simulation that not only imported the needed data for simulating but also
data concerning the whole model structure. Only a basic structure is
implemented and according to the data imported from the database the full
simulation model is created on resetting. This offers a high flexibility:
machines can be added and removed, parameters changed as well as the whole
course of manufacture only by editing the corresponding data in the database.
The data collected during simulation allows a precise analysis and comparison
of single simulation runs.
Monday 3:30:00 PM 5:00:00 PM
Manufacturing 3
Chair: Ed
Williams (University of Michigan, Dearborn)
Discrete Event Simulation in Automotive Final Process
System
Vishvas Patel, James Ashby, and John Ma (General Motors)
Abstract:
The Final Process System is an important part of the
entire quality assurance system in the automobile manufacturing process.
Operators and machines perform a series of crucial testing procedures before
shipping a vehicle. Many complex factors impact the system throughput. The
important ones are first time success rate, repair and service routing logic,
process layout, operator staffing, capacity of testing equipment and random
equipment breakdown. Discrete Event Simulation is a tool of choice in
analyzing these issues in order to develop an effective and efficient process
to ensure the system throughput. Using a case study from the automotive
industries, this paper discusses the methodology of modeling and studying the
Final Process System. The concepts and methods presented here are also
applicable to other discrete manufacturing processes.
A Simulation Study of an Automotive Foundry Plant
Manufacturing Engine Blocks
Sang D. Choi, Anil R. Kumar, and
Abdolazim Houshyar (Western Michigan University)
Abstract:
This paper discusses the initial efforts to implement
simulation modeling as a visual management and analysis tool at an automotive
foundry plant manufacturing engine blocks. The foundry process was modeled
using ProModel to identify bottlenecks and evaluate machine performance, cycle
times and production data (total parts, rejects, throughput, products/hr)
essential for efficient production control. Results from the current system
identified assembly machine work area as the bottleneck (although utilization
was greater than 95% for two assembly machines) resulting in high
work-in-process (WIP) inventory level, low resource and machine utilization.
Based on these results, optimal numbers were identified through use of
scenarios by varying the number of assembly machines and processing time of
each machine. In addition to these scenarios, strategies for production
control involving buffer sizes were also made.
Manufacturing Process Modeling of Boeing 747 Moving Line
Concepts
Roberto F. Lu and Shankar Sundaram (The Boeing Company)
Abstract:
Thousands of jobs performed on the Queen of the Sky,
the Boeing 747, final assembly line for each airplane. When the decision was
made to implement a moving line for the final assembly of the 747 it was
absolutely necessary to evaluate many aspects of these jobs. Discrete Event
Simulation models were constructed to analyze 747 final assembly moving line
scenarios throughout several phases. These models not only presented visual
understanding of different concepts, but also provided quantitative analysis
of suggested scenarios to the moving line team. The results are highly
optimized production flows and processes, reducing cost and flow time from the
traditionally 24 days to the targeted possible 18 days. This work outlines
some of the moving line concepts, modeling objectives, and simulation
analysis. Utilizations of different assembly positions were yielded as the
result of discrete simulation modeling of the 747 final assembly operation.
Tuesday 8:30:00 AM 10:00:00 AM
Transportation and Material
Handling
Chair: Chad DeJong (Intel Corporation)
Complexities of AGV Modeling in Newspaper Roll
Delivery System
Daniel J. Muller and Sarah M. Cardinal (Brooks-PRI
Automation, Inc.) and Juergen Baumbach (Swisslog Logistics Inc.)
Abstract:
Swisslog Logistics Inc., a leader in Automated Guided
Vehicle (AGV) technologies, proposed to update a major Northeastern newspaper
company’s AGV press delivery system. The project requirements included the
development of a simulation model to confirm the proposed vehicle quantity and
controls as well as evaluate the performance of the AGV system in response to
the following three operating scenarios: 1) Press Changeovers, 2) Peak
Production/Demand (3 Hours), 3) Weekly Production Schedule. The model provided
Swisslog and its customer with the capabilities to evaluate dynamic vehicle
scheduling, task priorities, press changeover requirements, vehicle routings
and battery charging logic. This paper shall present the concepts and
techniques used to model the detailed AGV components necessary to successfully
meet the project’s objectives.
Solving Logistics and Transportation Problems in a
Job Shop
Kambiz Farahmand and Arun Balasubramanian (Texas A&M
University)
Abstract:
A discrete event simulation model was developed to
study the flow of material and product in a shop floor. It uses real time data
available from a job shop solely dedicated to non-commercial contracts and as
such deals with very seasonal demand. The objective of this model is to
provide the shop with a decision support tool that will assist in evaluating
the movement of products throughout the shop. The simulation will be useful in
assessing the length of queues formed at each shop as well as in pointing out
bottlenecks. Actual operational and flow data are utilized in developing the
model. The simulation is implemented using the Arena software. In effect, the
model is to be used for a better understanding of operation of the shop floor
and better utilization of all the available resources.
Tuesday 10:30:00 AM 12:00:00 PM
Best Modeling Methods
Chair:
Marvin Seppanen (Productive Systems)
Virtual Factory – Highly Interactive
Visualisation for Manufacturing
Wolfgang Mueller-Wittig, Reginald
Jegathese, Meehae Song, Jochen Quick, Haibin Wang, and Yongmin Zhong (Nanyang
Technological University)
Abstract:
Funded by the Agency for Science, Technology and
Research - A*STAR - Singapore, CAMTech is collaborating with a Singaporean
research institute and two industry partners with the objective to improve
electronics assembly processes. The goal of this project is to visualise the
behaviour of an electronics assembly industry based on discrete events
simulation. The traditional scenario - from the customer placing order for a
product to delivery - goes through various phases including manufacturing the
product. Several major electronics manufacturing stages can be addressed:
fabrication, assembly, testing, and packing. Each of these stages accounts for
set up, process, failure, and wait time periods. A delay in one process will
accumulate over to the future delays. To simulate the discrete events a
general-purpose simulation system has been employed. For modelling and
visualisation CASUS (Computer Animation of Simulation Traces) system has been
used and refined developed by Fraunhofer Institute for Computer Graphics
(Fraunhofer-IGD).
Turn Lost Production Into Profit – Discrete Event
Simulation Applied on Resetting Performance in Manufacturing
Systems
Björn Johansson and Jürgen Kaiser (Chalmers University of
Technology)
Abstract:
World-class utilization of manufacturing resources is
of vital importance to any manufacturing enterprise in the global competition
of today. This requirement calls for superior performance of all processes
related to the manufacturing of products. One of these processes is the
resetting of machinery and equipment between two product runs, which will be
the focus area of this paper. This paper examines to what extent Discrete
Event Simulation (DES) can be applied to the evaluation of resetting
performance in manufacturing systems. For this purpose, a DES model of a
factory unit in Sweden is used for the research trials, derived from real
manufacturing situations. During the case study, DES has shown to be a
potential tool for the evaluation of resetting processes. The results from the
simulation runs provided valuable information for improvement initiatives.
Among other findings a solution is proposed, that turns losses into profit.
Documentation of Discrete Event Simulation Models
for Manufacturing System Life Cycle Simulation
Jan Oscarsson and
Matías Urenda Moris (University of Skövde)
Abstract:
The concept of life cycle simulation appeals to most
production engineers. There is a problem with simulation models of
manufacturing systems; they may be highly complex and time consuming to
develop. They embrace a considerable experience, which is gained through the
development process of the simulation model. It is therefore not enough to
develop an accurate simulation model. The model must be understood, updated,
reused and inhered by others. One way to achieve these goals could be through
use of a standardised documentation, which in turn explains the model and how
it has been developed. This paper presents a method for how simulation models
can be documented by standardised notations. The documentation is adapted to
different users of the simulation model.
Tuesday 1:30:00 PM 3:00:00 PM
Productivity Improvement
Chair:
Joe Hugan (Forward Vision)
Shifting Bottleneck Detection
Christoph
Roser, Masaru Nakano, and Minoru Tanaka (Toyota Central Research and
Development Laboratories)
Abstract:
This paper describes a novel method of calculating the
sensitivity of the manufacturing system throughput to the variables of the
machines. The sensitivity analysis needs only a single simulation, yet is easy
to use and provides accurate results. This sensitivity analysis is then used
to predict the change in the system throughput due to a change of the
variables of the machines provided that the system change does not
significantly change the bottleneck. These predictions can be used for a local
optimization, allowing the use of a steepest descent optimization algorithm.
The method is based on improving the momentary shifting bottlenecks. The
shifting bottlenecks are detected using the shifting bottleneck detection
method based on the active duration, i.e., the time a machine is active
without interruption. The method is easy to understand and easy to implement
in existing simulation software.
Throughput Sensitivity Analysis Using a Single
Simulation
Christoph Roser, Masaru Nakano, and Minoru Tanaka
(Toyota Central Research and Development Laboratories)
Abstract:
This paper describes a novel method of calculating the
sensitivity of the manufacturing system throughput to the variables of the
machines. The sensitivity analysis needs only a single simulation, yet is easy
to use and provides accurate results. This sensitivity analysis is then used
to predict the change in the system throughput due to a change of the
variables of the machines provided that the system change does not
significantly change the bottleneck. These predictions can be used for a local
optimization, allowing the use of a steepest descent optimization algorithm.
The method is based on improving the momentary shifting bottlenecks. The
shifting bottlenecks are detected using the shifting bottleneck detection
method based on the active duration, i.e., the time a machine is active
without interruption. The method is easy to understand and easy to implement
in existing simulation software.
Productivity Improvement in the Wood Industry Using
Simulation and Artificial Intelligence
Felipe F. Baesler, Milton
Moraga, and Francisco J. Ramis (Universidad del Bío-Bío)
Abstract:
The objective of this article is to present the results
obtained after using a simulation optimization methodology applied to a
production line from a secondary manufacturing wood processing plant of a well
known Chilean mill. For this reason a simulation model constructed in a
simulation software called ARENA, was integrated to a genetic algorithms
heuristic. The results obtained show that using a different configuration of
the plant resources, it is possible to reduce the total average cycle time in
approximately 18%. The resource configuration needed to reach this result was
obtained evaluating just 1.6% of the total number of possible combinations.
Tuesday 3:30:00 PM 5:00:00 PM
Manufacturing Modeling Architectures
Chair: Young Jun Son (University of Arizona)
Manufacturing Adapter of Distributed Simulation
Systems Using HLA
Hironori Hibino (JSPMI), Yoshiro Fukuda (Hosei
University), Yoshiyuki Yura (Shimizu Corporation), Keiji Mitsuyuki (Denso
Corporation) and Kiyoshi Kaneda (Makino Milling Machine Corporation)
Abstract:
In this research, the distributed simulation system to
easily evaluate a very large manufacturing system by synchronizing several
different simulators is developed. We designed the distributed simulation
system using High Level Architecture(HLA) as IEEE1516 standard. A
manufacturing adapter to connect manufacturing system simulators with HLA
using a plug-in style is proposed. The developed distributed simulation system
is confirmed using a case to evaluate a hypothetical manufacturing system
which produces motors. Three major commercial based manufacturing system
simulators as QUEST, SIMPLE++, and GAROPS are connected using the developed
manufacturing adapter. The storage model method to connect simulation models
and synchronize the simulators is used in the case study. The case study is
then carried out to evaluate the performance of the cooperative work.
An Architecture for a Generic Data-Driven Machine
Shop Simulator
Charles McLean, Al Jones, Tina Lee, and Frank
Riddick (NIST)
Abstract:
Standard interfaces could help reduce the costs
associated with simulation model construction and data exchange between
simulation and other software applications -- and thus make simulation
technology more affordable and accessible to a wide range of potential
industrial users. Currently, small machine shops do not typically use
simulation technology because of various difficulties and obstacles associated
with model development and data translation. This paper provides an overview
of work currently under way at the National Institute of Standards and
Technology (NIST) to develop a software architecture, standard data
interfaces, and a prototype generic machine shop simulator that can be
readily, reconfigured for use by a large number of small machine shops. It
also reviews prior work in this area and describes future work.
Architectural Concepts for a System Simulator for
Concurrent Prototyping of Equipment and Controls
K. Preston White,
Jr., Ryan Fritz, Stephen Horvath, Carlos Orellana, and Jonathan Wohlers
(University of Virginia) and Richard G. Fairbrother and William S. Terry
(Lockheed Martin Distribution Technologies)
Abstract:
AutoMod is a leading discrete-event simulation package
widely applied in the modeling and analysis of distribution systems. Included
in the AutoMod software suite is the Model Communications Module (MCM), which
allows an executing simulation to open socket connections and to send and
receive messages via TCP/IP network protocol. In this paper we report on a
pilot study which explores the functionality of the MCM. In particular, we
develop and implement an architecture that can be used to design, test,
verify, and optimize control system software interacting with a discrete-event
simulation of the system to be controlled. This architecture supports
concurrent engineering of controls and hardware prototypes. Application of
this architecture can significantly reduce the duration and cost of
development cycles for new equipment and systems. In addition, this
architecture can be applied to investigate the feasibility of implementing
engineering changes in systems currently deployed.
Wednesday 8:30:00 AM 10:00:00 AM
Manufacturing Modeling Methods
Chair: K. Preston White (University of Virginia)
Use of GI/G/1 Queuing Approximations to Set Tactical
Parameters for the Simulation of MRP Systems
S. T. Enns (University
of Calgary) and Sangjin Choi (Korea Institute of Energy Research)
Abstract:
There is a lack of prescriptive methods for setting lot
sizes and planned lead times effectively in MRP systems. Recent research has
suggested the application of queuing relationships. This study experimentally
investigates the use of GI/G/1 relationships for lot size selection along with
the use of exponentially smoothed feedback for dynamic planned lead time
setting. Results show that assumptions regarding lot interarrival time
variability have a large effect on lot sizes and performance.
Virtual Reality Simulation of a Mechanical Assembly
Production Line
Deogratias Kibira and Chuck McLean (National
Institute of Standards and Technology)
Abstract:
This paper presents our work on the application of
virtual- reality simulation to the design of a production line for a
mechanically-assembled product. The development of this simulation was
undertaken as a part of the Manufacturing Simulation and Visualization Program
at the National Institute of Standards and Technology in Gaithersburg, MD. The
major research problem is the partitioning and analysis of the assembly
operation of the prototype product into different tasks and allocation of
these tasks to different assembly workstations. Issues such as cycle times,
material handling and assembly line balancing complicate the problem. This
paper demonstrates the difficulties of using simulation modeling for
concurrent graphical simulation of assembly operations and discrete event
analysis of a production process in the same model. It also points out the
need to speed up the modeling process and reduce the level of effort required
in the construction of a simulation model.
An Approach and Interface for Building Generic
Manufacturing Kanban-Systems Models
Edward J. Williams (University
of Michigan - Dearborn), Onur M. Ülgen (University of Michigan) and Chris
DeWitt (Production Modeling Corporation)
Abstract:
Simulation of manufacturing systems, historically the
first major application area of discrete-event process simulation, is becoming
a steadily more proactive and important strategy for achieving manufacturing
efficiency. Concurrently, lean manufacturing has become a nearly essential
corporate strategy to compete successfully in an increasingly austere and
global business environment. Furthermore, industrial engineers responsible for
supporting successfully competitive manufacturing operations have less and
less time available for manipulating details deep within a simulation model in
order to evaluate numerous complex alternatives. Convergence among these
trends motivated the development of a generic manufacturing kanban-systems
simulator that has Kanban inventory optimization capability, and an
accompanying interface, described in this paper.
Wednesday 10:30:00 AM 12:00:00 PM
Simulation of Manufacturing
Operations
Chair: Cindy Schiess (Design Systems,
Inc.)
Optimum-Seeking Simulation in the Design and Control
of Manufacturing Systems: Experience with OptQuest for Arena
Paul
Rogers (University of Calgary)
Abstract:
This paper presents some of my experience in applying a
commercial optimum-seeking simulation tool to manufacturing system design and
control problems. After a brief introduction to both the general approach and
to the specific tool being used, namely OptQuest for Arena, the main body of
the paper reports on the use of the tool in tackling two manufacturing system
design and control problems, one very simple and one significantly more
complex. The paper concludes with some material highlighting how easy the tool
is to apply to this kind of problem and also presents some thoughts on how the
tool might be enhanced to improve its value.
Optimization of Operations in a Steel Wire
Manufacturing Company
Jai Thomas, Jayesh Todi, and Asif Paranjpe
(Western Michigan University)
Abstract:
The project was conducted in a high quality steel wire
manufacturing company with the production capacity of over 120,000
tones/annum. The wire drawn from the high speed wire drawing (KOCH) machine is
fed as the raw material for BEKEART (zinc coating galvanization) furnace. The
problem faced by the company is the variability in the amount of input to the
furnace, which results from the breakdowns occurring on the KOCH machine
resulting in low production. Any downtime in the process occurring at the KOCH
machine adversely affects the productivity of the BEKEART furnace, as a result
of which the total production on this line suffers and hence the profits of
the company. Simulation study was done with the objective of increasing the
throughput and ensuring smooth product flow through the system by finding the
optimum arrival batch size.
Optimization of Buffer Sizes in Assembly Systems Using
Intelligent Techniques
Fulya Altiparmak and Berna Dengiz (Gazi
University) and Akif A. Bulgak (Concordia University)
Abstract:
When the systems under investigation are complex, the
analytical solutions to these systems become impossible. Because of the
complex stochastic characteristics of the systems, simulation can be used as
an analysis tool to predict the performance of an existing system or a design
tool to test new systems under varying circumstances. However, simulation is
extremely time consuming for most problems of practical interest. One approach
to overcome this limitation is to develop a simpler model to explain the
relationship between the inputs and outputs of the system. Simulation
metamodels are increasingly being used in conjunction with the original
simulation, to improve the analysis and understanding of decision-making
processes. In this study, artificial neural networks (ANN) metamodel is
developed for simulation model of an asynchronous assembly system and ANN
metamodel together with simulated annealing (SA) is used to optimize the
buffer sizes in the system.
![]()