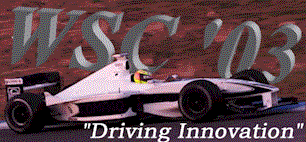 |
WSC 2003 Final Abstracts |
Simulation-Based Scheduling Track
Monday 10:30:00 AM 12:00:00 PM
Supply Chain Planning
Chair:
Peter Lendermann (Singapore Institute of Manufacturing Technology)
Rolling Horizon Scheduling of Multi-Factory Supply
Chains
Eunkyoung G. Cho, Kristin A. Thoney, Thom J. Hodgson, and
Russell E. King (North Carolina State University)
Abstract:
The Virtual Factory is a job shop scheduling tool that
was developed at NC State. It has been found to provide near-optimal solutions
to industrial-sized problems in seconds. Recently, the Virtual Factory was
expanded to include inter-factory transportation operations which enabled the
detailed scheduling of entire multi-factory manufacturing supply chains.
Separately, a rolling horizon procedure was developed to test the Virtual
Factory for single factory problems. This procedure allowed us to more
accurately predict how the Virtual Factory would perform in industry.
Consequently, the rolling horizon procedure was extended to multi-factory
settings to gauge industrial performance and eliminate transient effects found
in previous multi-factory experimentation. Experimental results, under a
variety of different scenarios, indicate that the Virtual Factory also
performs well in multi-factory, rolling horizon settings.
A Reinforcement Learning Approach to Production
Planning in the Fabrication/Fulfillment Manufacturing Process
Heng
Cao (IBM T.J. Watson Research Center), Haifeng Xi (IBM T.J. Watson Research)
and Stephen F. Smith (Carnegie Mellon University)
Abstract:
We have used Reinforcement Learning together with Monte
Carlo simulation to solve a multi-period production planning problem in a
two-stage hybrid manufacturing process (a combination of build-to-plan with
build-to-order) with a capacity constraint. Our model minimizes inventory and
penalty costs while considering real-world complexities such as different
component types sharing the same manufacturing capacity, multi-end-products
sharing common components, multi-echelon bill-of-material (BOM), random lead
times, etc. To efficiently search in the huge solution space, we designed a
two-phase learning scheme where “good” capacity usage ratios are first found
for different decision epochs, based on which a detailed production schedule
is further improved through learning to minimize costs. We will illustrate our
approach through an example and conclude the paper with a discussion of future
research directions.
Theory and Practice of Advanced Planner and
Optimizer in Supply Chain Domain
Sam Bansal (International
Management Consultant)
Abstract:
This paper describes the Supply Chain Management
do-main of SAP. It further describes how the SAP APO, the Advanced Planner
& Optimization tool set fits in the over-all domain of SCM. The founding
principles of APO are also presented. Various algorithms used as part of
planning & optimization are presented, as well as their relationships with
simulation techniques.
Monday 1:30:00 PM 3:00:00 PM
Factory Scheduling
Chair: Juergen
Potoradi (Infineon Technologies AG)
Simulation based Scheduling Using a Two-Pass
Approach
Chin Soon Chong, Appa Iyer Sivakumar, and Robert Gay
(Nanyang Technological University)
Abstract:
Bottleneck based scheduling is a popular approach in
production scheduling, and it has achieved promising results in industry. To
incorporate this approach in discrete event simulation tools is difficult
since the approach requires multiple passes, forward and backward, to reach a
good solution for the scheduling problem. In this paper, we propose a two-pass
scheduling approach using discrete-event simulation that takes bottlenecks
into consideration. In the first pass, a simulation run is performed and
bottlenecks are determined. If significant bottlenecks are identified, a
second-pass simulation is performed to reduce the loading on bottlenecks
through specific scheduling strategies.
Implementing a Simulation-Based Scheduling System
for a Two-Plant Operation
Jeffrey A. Joines, Andrew W. Sutton,
Kristin Thoney, Russell E. King, and Thom J. Hodgson (North Carolina State
University)
Abstract:
Scheduling any complicated job shop becomes
increasingly more difficult when the cycle time is reduced. This paper will
discuss the implementation of a simulation-based scheduling system that
properly schedules parts in a two-plant operation. The system has allowed the
company to reduce the cycle time by at least a week from two/three weeks to
one/two weeks. As part of the project, the generation of the input data needed
to drive the simulation is also discussed since this data did not exist in the
correct form. The model generation, simulation development, and
experimentation will be discussed. The system that is described is currently
being used to generate the schedules.
Simulation-Based Finite Scheduling at Albany
International
Juha-Matti Lehtonen and Patrik Appelqivst (Helsinki
University of Technology) and Teemu Ruohola and Ilkka Mattila (Delfoi Ltd.)
Abstract:
Simulation-based production scheduling approaches are
emerging as alternatives to optimization and simpler approaches such as
priority rules. This paper presents an application of a simulation-based
finite scheduling at Albany International, the largest manufacturer of paper
machine clothing in the world. Simulation is used as a decision support tool
for manual schedule creation. User experiences have been encouraging. We argue
that an optimization-based approach is not necessarily the most economical and
identify a number of tentative key enablers of a simulation-based solution.
The case indicates that a simulation-based solution is a viable option when
the production process does not include combination of materials and local
sequencing is adequate. A simulation-based solution capitalizes on this
existing source of tacit knowledge by giving expert human schedulers tools for
testing and improving schedules.
Monday 3:30:00 PM 5:00:00 PM
Dynamic Scheduling I
Chair: Sam
Bansal (International Management Consultant)
Real-Time Decision Making Using
Simulation
Mukesh Dalal, Brett Groel, and Armand Prieditis
(LookAhead Decisions Inc.)
Abstract:
Based on a discrete-event simulation model,
Simulation-based Real-time Decision-Making (SRDM) is an innovative approach to
real-time, goal-directed decision-making. When applied to a flexible
manufacturing system, SRDM makes better decisions than most fixed policies,
such as deterministic, stochastic and manual. SRDM even improves over
machine-enhanced policies that have been optimized over several hours using a
tool such as OptQuest. Compared to these fixed policies, SRDM shows greater
improvement for more complex systems and is quite robust with respect to
modeling errors. SRDM can handle the unexpected, because it avoids the
rigidity and myopia caused by fixed policies. Since most real-time decisions
in currently deployed manufacturing systems are made either manually or by
using fixed policies, our results suggest that using SRDM instead could lead
to significant improvement in operating performance.
Simulation-Based Scheduling for Dynamic Discrete
Manufacturing
Chin Soon Chong, Appa Iyer Sivakumar, and Robert Gay
(Nanyang Technological University)
Abstract:
A simulation-based real-time scheduling mechanism for
dynamic discrete manufacturing is presented in this paper. Modified mean flow
time performance for different scheduling approaches is compared through
off-line simulation experiments, under dynamic manufacturing environments that
are subjects to disturbances such as machine breakdowns. These experimental
results are used as reference indices for the real-time scheduling mechanism
to select the better scheduling approaches for further evaluation based on the
actual manufacturing conditions. Discrete-event simulation is used on-line to
evaluate the selected approaches and the corresponding schedules to determine
the best solution. The selected schedule is used until the deviation of actual
performance from the estimated one exceeds a given limit, or when a major
event occurs. A new simulation is then performed with the remaining operations
to select a new schedule.
Use of Discrete Event Simulation to Analyze
Dispatch Policies of an Equipment Group in Semiconductor Fab
Raja
Sunkara and Ramesh Rao (National Semiconductor Corp.)
Abstract:
This article describes a methodology to model complex
operation and process driven practices using a discrete event simulator. This
level of detail in the model is critical for the analyses and design of
complex operation and process driven dispatch policies in a semiconductor fab.
The modeling of these practices is typically not a part of the general set of
rules and methods provided by commercially available simulation software. The
methodology provides key information that simplifies the development of
suitable dispatch policies subject to factory dynamics. The modeling
philosophy plays a key role in the success of simulation as a culture. As an
example, we present the modeling of complex floor practices to analyze the
impact of setup changes subject to process restrictions.
Tuesday 8:30:00 AM 10:00:00 AM
Dynamic Scheduling II
Chair:
Leon McGinnis (Georgia Tech)
Look-Ahead Strategies for Controlling Batch Operations
in Industry – An Overview
Durk-Jouke van der Zee (University of
Groningen)
Abstract:
Batching jobs in a manufacturing system is a very
common policy in most industries. Main reasons for batching are avoidance of
set ups and/or facilitation of material handling. Examples of batch-wise
production systems are ovens found in aircraft industry and in semiconductor
manufacturing. Starting from the early nineties much research efforts have
been put in constructing strategies for the dynamic control of these systems
in order to reduce cycle times. Typically, these so-called `look-ahead
strategies' base their scheduling decision on the information on a few near
future product arrivals. In this paper we give a literature overview of the
developed strategies, consider basic insights in their construction and
highlight issues for further research.
SIMUL8-Planner Simulation-Based Planning and
Scheduling
Kieran H. Concannon, Kim I. Hunter, and Jillian M.
Tremble (Visual8 Corporation)
Abstract:
This paper provides an introduction to the technique of
simulation-based production planning and scheduling, a fast growing and
popular area in the simulation industry. SIMUL8 and Visual8 Corporations have
collaborated to develop a new software application called SIMUL8-Planner that
assists in the development of this type of system. The following document
outlines some of the requirements, advantages, and features within this
exciting new product.
Fast Simulation Model for Grid Scheduling
Using HyperSim
Sugree Phatanapherom and Putchong Uthayopas
(Kasetsart University) and Voratas Kachitvichyanukul (Asian Institute of
Technology)
Abstract:
To develop grid scheduling algorithms, a high
performance simulator is necessary since grid is an uncontrollable and
unrepeatable environment. In this paper, a discrete event simulation library
called HyperSim is used as extensible building blocks for grid scheduling
simulator. The use of event graph model for the grid simulation are proposed.
This model is well supported by HyperSim which yields a very high performance
simulation. The experiments are conducted to compare HyperSim with other
several simulators in terms of speed and scalability. The result shows a
significant simulation speed improvement over many widely used simulators.
Furthermore, sample simulation results of basic job scheduling problem are
shown to com-pare to well-known heuristics.
![]()