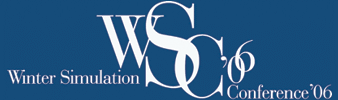 |
WSC 2006 Abstracts |
Simulation-Based Scheduling Track
Monday 10:30:00 AM 12:00:00 PM
Simulation-Based Scheduling I
Chair: Jennifer Bekki (Arizona State University)
Sequence Step Algorithm for Continuous Resource
Utilization in Probabilistic Repetitive Projects
Photios G. Ioannou
and Chachrist Srisuwanrat (University of Michigan)
Abstract:
The sequence step algorithm addresses for the first
time the problem of scheduling repetitive projects with probabilistic activity
durations while maintaining continuous resource utilization. This algorithm is
based on generalized concepts that can be implemented in most general-purpose
simulation systems. The algorithm is presented in detail and is applied to an
example project with 7 activities and 4 repetitive projects using a simulation
model developed in Stroboscope, an activity-based simulation system. Numerical
and graphical results help explain the algorithm and provide insight into the
underlying tradeoff problem between reducing the expected crew idle time and
increasing the expected project duration.
Simulation-Based Scheduling System in a
Semiconductor Backend Facility
Sven Horn and Gerald Weigert
(Dresden University of Technology), Sebastian Werner (Infineon Technologies)
and Thomas Jähnig (Qimonda)
Abstract:
The semiconductor manufacturing process is usually
divided in two parts: frontend and backend. In contrast to the frontend, where
the manufacturing process is dominated by cluster-tools and cyclic routes, the
backend has a predominant linear structure. In contrast to the frontend flow
which is mostly controlled by dispatch rules, the backend process is suitable
for real scheduling. A scheduling system for the backend of Infineon
Technologies Dresden based on a Discrete Event Simulation (DES) system was
developed and tested in the real industrial environment. The simulation model
is automatically generated from the databases of the manufacturer. The system
is used for short term scheduling - from one shift up to one week. The paper
will focus on the aspect of optimizing the process flow and calculating exact
release dates for lots. The basic principles are applicable not only in the
semiconductor industry but also in other industrial sectors.
Pareto Control in Multi-Objective Dynamic
Scheduling of a Stepper Machine in Semiconductor Wafer
Fabrication
Amit Kumar Gupta (SIMTech) and Sivakumar Appa Iyer
(Singapore-MIT Alliance, NTU)
Abstract:
This paper focuses on Pareto control in multi-objective
dynamic scheduling of a stepper machine that is considered as a bottleneck
machine in the semiconductor wafer fabrication process. We propose the use of
compromise programming method for achieving Pareto control in the needs of
conflicting objectives such as mean cycle time, cycle time variance and
maximum tardiness. Using conjunctive simulated scheduling, at each decision
instance in simulated time, a Pareto job is selected and loaded on the machine
for processing. Using the real factory data, we demonstrate the concept of
Pareto control in dynamic scheduling and show how a stepper machine can be
controlled at specified needs of scheduling objectives. The results obtained
from Pareto control approach are superior to the simulated results of actual
operating heuristic in the factory.
Monday 1:30:00 PM 3:00:00 PM
Simulation-Based Scheduling II
Chair: Gerald Weigert (Technische University
Dresden)
Simulation-Based Multi-Objective Optimization of a
Real-World Scheduling Problem
Anna Persson, Henrik Grimm, Amos Ng,
and Thomas Lezama (Centre for Intelligent Automation) and Jonas Ekberg,
Stephan Falk, and Peter Stablum (Posten AB)
Abstract:
This paper presents a successful application of
simulation-based multi-objective optimization of a complex real-world
scheduling problem. Concepts of the implemented simulation-based optimization
architecture are described, as well as how different components of the
architecture are implemented. Multiple objectives are handled in the
optimization process by considering the decision makers’ preferences using
both prior and posterior articulations. The efficiency of the optimization
process is enhanced by performing culling of solutions before using the
simulation model, avoiding unpromising solutions to be unnecessarily processed
by the computationally expensive simulation.
A Reinforcement Learning Algorithm to Minimize
the Mean Tardiness of a Single Machine with Controlled
Capacity
Hadeel D. Idrees, Mahdy O. Sinnokrot, and Sameh Tawfiq
Al-Shihabi (University of Jordan)
Abstract:
In this work, we consider the problem of scheduling
arriving jobs to a single machine where the objective is to minimize the mean
tardiness. The scheduler has the option of reducing the processing time by
half through the employment of an extra worker for an extra cost per job
(setup cost). The scheduler can also choose from a number of dispatching
rules. To find a good policy to be followed by the scheduler, we implemented a
lambda-SMART algorithm to do an on-line optimization for the studied system.
The found policy is only optimal with respect to the state representation and
set of actions available, however, we believe that the developed policies are
easy to implement and would result in considerable savings as shown by the
numerical experiments conducted.
Stochastic Shipyard Simulation with
SimYard
Oliver Dain, Matthew Ginsberg, Erin Keenan, John Pyle,
Tristan Smith, and Andrew Stoneman (On Time Systems) and Iain Pardoe
(University of Oregon)
Abstract:
SimYard is a stochastic shipyard simulation tool
designed to evaluate the labor costs of executing different schedules in a
shipyard production environment. SimYard simulates common production problems
such as task delays and labor shortages. A simulated floor manager reacts to
problems as they arise. Repeatedly simulating multiple schedules allows the
user to compare the schedules on many different metrics, such as expected
labor costs and the probability of missing the deadline. A SimYard simulation
is driven by many inputs that describe the shipyard being simulated.
Determining the correct values for these inputs can be framed as a
multivariate calibration problem, which can be solved using inverse regression
methods. Predictive sampling from the resulting model provides an appropriate
adjustment for statistical uncertainty.
Monday 3:30:00 PM 5:00:00 PM
Simulation-Based Scheduling III
Chair: Gerald Mackulak (Arizona State University)
SIMUL8-Planner for Composites Manufacturing
Center
Kim Hindle and Matt Duffin (Visual8 Corporation)
Abstract:
SIMUL8-PLANNER is a simulation-based planning and
scheduling tool that intelligently sequences product flow across the plant.
Combining order planning with production modeling, SIMUL8-PLANNER can generate
production schedules that satisfy delivery objectives and capacity limits.
This paper examines a case study where the SIMUL8-PLANNER tool was used to
answer the complex scheduling problem of sequencing part requirements through
a Composites Manufacturing Center. First a production model was used to
capture the current workings of plant processes and product flow. Next, a
sequencing system was added to the production model in order to provide a
powerful, flexible, and adaptive scheduling system for all of the work cells
and machines within the facility, complete with links to the company's ERP /
shop-floor data systems. SIMUL8-Planner provides a practical approach and
powerful platform for developing, testing, and refining production schedules
before they are released to the shop-floor in a virtual and risk-free setting.
It offers a flexible and open scheduling system that can be used for a wide
range of production scheduling applications.
Simulation Assisted Optimization and Real-Time
Control Aspects of Flexible Production Systems Subject to
Disturbances
Kiran R Mahajan, Wilhelm Dangelmaier, Thomas Seeger,
Benjamin Klöpper, and Mark Aufenanger (Heinz Nixdorf Institute, University of
Paderborn)
Abstract:
Several types of production systems have been studied
and researched in the past using either simulation and\or optimization
methods. In this paper we describe the design and development of a simulation
assisted predictive-reactive system for scheduling and rescheduling a typical
flexible production system configuration. Aspects like the combined use of
simulation and optimization to solve complex scheduling and rescheduling tasks
are described in view of system stability and some of the broader production
system elements like buffer sizing and material handling equipment. Results
show that combining simulation and optimization for predictive scheduling
resulted in better and valid performance measures for a typical example.
Results show that some newly addressed aspects of stability and real-time
control can be handled efficiently using a combination of simulation and
optimization. Our discussions only bolster the claim that simulation is an
indispensable tool in managing complex production systems.
![]()