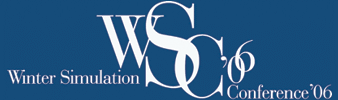 |
WSC 2006 Abstracts |
Semiconductor Manufacturing Track
Tuesday 8:30:00 AM 10:00:00 AM
Factory Simulation
Chair: Lars
Mönch (University of Hagen)
Estimating Expected Completion Times with
Probabilistic Job Routing
Nirmal Govind (Intel Corporation) and
Theresa M Roeder (San Francisco State University)
Abstract:
A common problem in production environments is the need
to estimate the remaining time in system for work-in-progress jobs. Simulation
can be used to obtain the estimates. However, when the future path of a job is
uncertain (due to stochastic events such as rework), using simulation to
estimate the remaining cycle time of a job at step k can be imprecise;
traditional confidence intervals on the estimated remaining cycle times may be
too large to be of practical significance. We propose a response surface
methodology-based approach to estimating conditional confidence intervals on
the remaining cycle times as jobs progress through the system and more
information is obtained on them. This method will provide more useful and
accurate estimates of remaining cycle times at various stages of the process
flow. Further, we outline two different simulation approaches for estimating
the response surfaces used to generate the confidence intervals.
Modeling Semiconductor Tools for Small Lotsize
Fab Simulations
Kilian Schmidt (Advanced Micro Devices), Oliver
Rose (Dresden University of Technology) and Joerg Weigang (Advanced Micro
Devices)
Abstract:
Short cycle times are critical to the success of
semiconductor manufacturing. The addition of more and more mask layers leads
to higher raw process times and makes short cycle times an increasingly
challenging task. One cycle time reduction possibility semiconductor
manufacturers now look at is lotsize reduction. A reduction in lotsize
transfers directly into lower raw process times. Modeling and simulation are
key to assess opportunities and risks of such an approach. This paper looks at
the implications that follow from small lotsizes for tool models used for the
assessment.
Economy of Scale Effects for Larger Wafer
Fabs
Oliver Rose (Dresden University of Technology)
Abstract:
In this paper, we present the results of a simulation
study for semiconductor wafer fabrication facilities (wafer fabs) where we
multiplied the number of tools per tool group and the number of operators. We
were interested in the effects on the product cycle times when we keep the fab
utilization constant while increasing the size of the tool groups by constant
factors, i.e., forming so-called giga fabs. It turns out, that the drop in
cycle time is considerable.
Tuesday 10:30:00 AM 12:00:00 PM
Performance Analysis in Semiconductor
Manfacturing
Chair: John Fowler (Arizona State University)
Simulation Analysis on the Impact of Furnace Batch
Size Increase in a Deposition Loop
Boon Ping Gan and Peter
Lendermann (Singapore Institute of Manufacturing Technology) and Kelvin Paht
Te Quek, Bart van der Heijden, Chen Chong Chin, and Choon Yap Koh (Systems on
Silicon Manufacturing Co. Pte. Ltd.)
Abstract:
In the dynamic environment of semiconductor
manufacturing operations, a bottleneck could be created at the bake furnaces
of the deposition loop as capacity expands. Upgrading of the bake furnaces by
adding a lot-per-batch in the boat or purchasing a new furnace are two
possible solutions to this problem. A simulation model was constructed to
assist the decision making, with the behavior of the wet benches (upstream
tools) and cluster tools (downstream tools) being modeled in detail. We
concluded that a limited number of furnaces upgrade is sufficient to sustain
the capacity expansion. But the bottleneck was shifted to an upstream tool,
which required the backup tool to be activated to manage the queue. A loading
policy that constrains batches to queue at maximum time before loading into
the furnaces has to be implemented to balance the efficiency at the furnaces
and their downstream tools, without compromising on the cycle time.
Indirect Cycle-Time Quantile Estimation for
Non-FIFO Dispatching Policies
Jennifer M. Bekki and Gerald T
Mackulak (Arizona State University) and John W Fowler (Arizona State
Ubiversity)
Abstract:
Previous work has shown that the Cornish-Fisher
expansion (CFE) can be used successfully in conjunction with discrete event
simulation models of manufacturing systems to estimate cycle-time quantiles.
However, the accuracy of the approach degrades when non-FIFO dispatching rules
are employed for at least one workstation. This paper suggests a modification
to the CFE-only approach which utilizes a power data transformation in
conjunction with the CFE. An overview of the suggested approach is given, and
results of the implemented approach are presented for a model of a
non-volatile memory factory. Cycle-time quantiles for this system are
estimated using the CFE with and without the data transformation, and results
show a significant accuracy improvement in cycle-time quantile estimation when
the transformation is used. Additionally, the technique is shown to be easy to
implement, to require very low data storage, and to allow easy estimation of
the entire cycle-time cumulative distribution function.
A Full Factory Transient Simulation Model for the
Analysis of Expected Performance in a Transition Period
Moti Klein
and Adar Kalir (Intel)
Abstract:
Intel’s Fab-18 is based in Israel, and has transitioned
from producing 0.18-micron logic devices to producing 90nM flash products.
During this transition period, the factory has de-ramped in volume of logic
while ramping-up flash. AutoSched AP software was utilized for the development
of a transient simulation model of the Fab’s behavior during this period. It
is the first attempt, at Intel, to utilize a full factory simulation in order
to analyze and support decisions that pertain to a transient period of
parallel de-ramp and ramp-up of technologies. Unlike typical simulation models
for the analysis of factory performance and behavior in steady-state, the
transient model poses several modeling challenges and requires major
adjustments in dealing with these challenges. In this paper, we discuss those
aspects. The benefits and contribution of such a model to decision making and
the improvement of factory performance are also presented.
Tuesday 1:30:00 PM 3:00:00 PM
Dispatching and Scheduling
Approaches
Chair: Daniel Quadt (Infineon Technologies AG)
The Use of Slow Down Factors for the Analysis and
Development of Scheduling Algorithms for Parallel Cluster
Tools
Robert Unbehaun and Oliver Rose (Dresden University of
Technology)
Abstract:
In this paper, we describe the problem of developing
scheduling algorithms for an environment of parallel cluster tools, which is a
special case of the parallel unrelated machines problem. At first we will
describe the problem under consideration in detail and then present our
scheduling environment and the idea of using slow down factors to predict lot
cycle times to evaluate schedules and parts of them. This article is more a
conceptual kind of work containing mostly basic thoughts to illustrate facets
of the problem and first solution ideas. Nonetheless the authors see a high
potential in examining these questions. Little research has been done on that
issue so far.
Simulation-Based Selection of Machine
Criticality Measures for a Shifting Bottleneck Heuristic
Jens
Zimmermann and Lars Moench (FernUniversitaet in Hagen)
Abstract:
In this paper, we investigate the influence of several
machine criticality measures on the performance of a shifting bottleneck
heuristic for complex job shops. The shifting bottleneck heuristic is a
decomposition approach that tackles the overall scheduling problem by solving
a sequence of tool group scheduling problems and compose the overall solution
by using a disjunctive graph. Machine criticality measures are responsible for
the sequence of the considered tool group scheduling problems. We suggest a
new machine criticality measure that is a weighted sum of several existing
criticality measures. It turns out that the shifting bottleneck heuristic
performs well compared to dispatching rules when the suggested criticality
measure is used. We present the results of computational experiments.
Tuesday 3:30:00 PM 5:00:00 PM
Planning Approaches in Semiconductor
Manfacturing
Chair: Oliver Rose (Dresden University of Technology)
Using System Dynamics Simulations to Compare Capacity
Models for Production Planning
Seza Orcun and Reha Uzsoy (Purdue
University) and Karl Kempf (Intel Corporation)
Abstract:
While a variety of optimization formulations of
production planning problems have been proposed over the last fifty years, the
majority of these are based on simple models of capacity that fail to reflect
the nonlinear relationship between workload and lead times induced by the
queuing behavior of capacitated production resources. We use system dynamics
simulations of a simple capacitated production system to examine the
performance of several different capacity models that yield load-dependent
lead times, and relate these models to those used in system dynamics models of
production systems.
Flexible Experimentation and Analysis for Hybrid
DEVS and MPC Models
Dongping Huang, Hessam S. Sarjoughian, Daniel
E. Rivera, and Gary W. Godding (Arizona State University) and Karl G. Kempf
(Intel Corporation)
Abstract:
Discrete-event simulation and control-theoretic
approaches lend themselves to studying semiconductor manufacturing
supply-chain systems. In this work, we detail a modeling approach for
semiconductor manufacturing supply-chain systems in a hybrid DEVS/MPC testbed
that supports experimentations for DEVS and MPC models using DEVS/MPC KIB.
This testbed supports detailed analysis and design of interactions between
discrete processes and tactical controller. A set of experiments have been
devised to illustrate the role of modeling interactions between Discrete Event
System Specification and Model Predictive Control models. The testbed offers
novel features to methodically identify and analyze complex model interactions
and thus support alternative designs based on tradeoffs between model
resolutions and execution times.
An Analytical Model of Vehicle-Based Automated
Material Handling Systems in Semiconductor Fabs
Dima Nazzal
(University of Central Florida) and Leon F. McGinnis (Georgia Institute of
Technology)
Abstract:
This research explores analytical models useful in the
design of vehicle-based Automated Material Handling Systems (AMHS) to support
semiconductor manufacturing. The objective is to correctly estimate the
throughput and move request delay. This analysis proposes a computationally
effective analytical approach to multi-vehicle AMHS performance modeling for a
simple closed loop. A probabilistic model is developed, based on a detailed
description of AMHS operations, and the system is analyzed as an extended
Markov chain. The model tracks the operations of one vehicle on the
closed-loop considering the possibility of vehicle-blocking. This analysis
provides the essential parameters such as the blocking probabilities in order
to estimate the performance measures. A numerical example is analyzed and
simulated using Automod to demonstrate and validate the queuing model.
Wednesday 8:30:00 AM 10:00:00 AM
Modeling Approaches for Wafer
Fabs
Chair: Leon McGinnis (Georgia Institute of Technology)
Systems Engineering and Design of High Tech
Factories
Leon McGinnis, Edward Huang, and Kan Wu (Georgia
Institute of Technology)
Abstract:
Contemporary technology for Product Lifecycle
Management (PLM) integrates computer aided design (CAD) and engineering
analysis (CAE) to support rapid, distributed, team-oriented product data
development and management, including high fidelity simulation on demand. This
technology potentially provides a platform for creating a new generation of
factory design tools which enable “on demand” simulation and analytic model
results to be used by factory designers. This paper describes the opportunity,
and provides an illustration in the context of semiconductor wafer fab design.
Simulation-Based Scheduling of Parallel
Wire-Bonders with Limited Clamp&Paddles
Daniel Quadt (Infineon
Technologies AG)
Abstract:
We present a scheduling procedure for the wire-bonding
operation of a semiconductor assembly facility. The wire-bonding operation
typically consists of a large number of unrelated parallel machines and is
typically one of the bottlenecks in an assembly facility. The scheduling
procedure is able to handle setup times, limited fixtures (clamp&paddles)
and non-zero machine ready-times (initial work in progress). It is based on a
simulator that generates a schedule and a Simulated Annealing approach to
optimize the schedule. Some preliminary results from an implementation in a
large assembly facility are given.
![]()