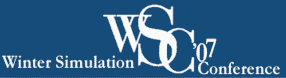 |
WSC 2007 Final Abstracts |
Semiconductor Manufacturing Track
Tuesday 1:30:00 PM 3:00:00 PM
Modeling and Analysis of Semiconductor
Manufacturing
Chair: John Fowler (Arizona State University)
Improved Simple Simulation Models for Semiconductor
Wafer Factories
Oliver Rose (Dresden University of Technology)
Abstract:
Semiconductor wafer fabrication facilities (wafer fabs)
are among the most complex production facilities. A large product variety,
hundreds of processing steps per product, hundreds of machines of different
types, and automated transport lead to a system complexity which is hard to
understand and hard to handle. For educating planners and developing adequate
material flow control mechanisms, simple models for this complex environment
are required. Several years ago, we published some first approaches which were
useful to explain the fab behavior after a serious bottleneck breakdown. With
that simple model, however, it was only possible to predict the cycle time
distribution of the lots for a few scenarios. In this paper, we present some
model improvements which lead to a rather good cycle time prediction for a
variety of load situations.
Simulation Framework for Complex Manufacturing
Systems with Automated Material Handling
Rene Driessel and Lars
Moench (University of Hagen)
Abstract:
In this paper, we suggest a framework that allows for
the simulation-based performance assessment of complex manufacturing systems
with Automated Material Handling Systems (AMHS). Therefore, we consider a
coupling architecture that connects simulation models of the manufac-turing
base system and the AMHS with a shop-floor control system. The center point of
this architecture is a blackboard-type data layer between the shop-floor
control system and the two simulation engines. We provide detailed information
on how the different subsystems communicate and how each system triggers
events of the other systems. We show by means of a case study how this
framework supports the required performance assessment.
Using Quantiles in Ranking and Selection
Procedures
Jennifer M. Bekki, John W. Fowler, and Gerald T.
Mackulak (Arizona State University) and Barry L. Nelson (Northwestern
University)
Abstract:
A useful performance measure on which to compare
manufacturing systems is a quantile of the cycle time distribution.
Unfortunately, aside from order statistic estimates, which can require
significant data storage, the distribution of quantile estimates has not been
shown to be normally distributed, violating a common assumption amongst
ranking-and-selection (R&S) procedures. To address this, we provide
empirical evidence supporting an approach using the mean of a group of
quantile estimates as the comparison measure. The approach is detailed and
illustrated through experimentation on four M/M/1 queues in which the 0.9
cycle-time quantile is the performance measure. Results in terms of simulation
effort and accuracy are reported and compared to results obtained using the
macro-replications approach for inducing normality as well as to results
obtained by applying R&S procedures to quantile estimates directly. The
suggested procedure is shown to provide significant savings in simulation
effort while sacrificing very little in accuracy.
Tuesday 3:30:00 PM 5:00:00 PM
Semiconductor Manufacturing Performance
Improvement
Chair: Lars Moench (Technical University of Ilmenau)
Application of Combined Discrete-event Simulation
and Optimization Models in Semiconductor Enterprise Manufacturing
Systems
Gary Godding and Hessam Sarjoughian (Arizona State
University) and Karl Kempf (Intel Corporation)
Abstract:
It is a common practice to use simulation for
validating different types of control and planning algorithms. However, the
science of how to rigorously integrate simulation and decision models is not
well understood and becomes critically important as the complexity and scale
of these models increase. In our research, we have developed a methodology for
integrating different types of models using a Knowledge Interchange Broker
(KIB). In this paper we describe a supply-chain semiconductor application
where the KIB has been used as an integral part of developing and deploying a
commercial Model Predictive Control model for use in operating a multi-billion
dollar supply chain. The simulation based experiments facilitated developing
and validating the controller design and data automation for a real-world
semiconductor manufacturing system.
Simulation Experimental Investigation on Job Release
Control in Semiconductor Wafer Fabrication
Chao Qi (Singapore-MIT
Alliance), Appa Iyer Sivakumar (School of Mechanical and Aerospace
Engineering) and Stanley B. Gershwin (Massachusetts Institute of Technology)
Abstract:
This paper presents a new job release methodology,
WIPLOAD Control, especially in semiconductor wafer fabrication environment.
The performance of the proposed methodology is evaluated in a simulation study
on a simplified wafer fabrication model, in comparison with other existing
release control methodologies. A case study is also conducted by simulating a
real-life wafer fabrication facility. Based on the experimental results, it
appears that WIPLOAD Control is a reliable job release methodology, which can
efficiently reduce average cycle time and standard deviation of cycle time for
a given throughput level, especially with the increase of system congestion
level and system variability caused by stochastic events such as machine
unreliability or processing time variability.
Sensitivity Analysis on Causal Events of WIP
Bubbles by a Log-driven Simulator
Ryo Hirade, Rudy Raymond, and
Hiroyuki Okano (IBM Research)
Abstract:
Fluctuations of work-in-progress (WIP) levels cause
variability of cycle time and often lead to productivity losses in
semiconductor wafer fabrication plants. To identify sources of such
variability, we are developing a root cause analysis tool with history logs of
operational events, such as high WIP or equipment downtime, as inputs to
automatically find the chains of events that create the variability. In the
root cause analysis, one of the key steps is to aggregate the observed events
into groups that are likely in cause-effect relationships. For operational
events that involve time lags in cause-effect relationships, grouping the
events requires identification of the time windows of causality based on
discrete event simulations. This paper describes a design and implementation
of a simulator for this purpose. The simulator does not assume any statistical
or mathematical model, and thus is simple to
maintain.
Wednesday 8:30:00 AM 10:00:00 AM
Semiconductor Manufacturing Equipment
Modeling
Chair: Nirmal Govind (Intel
Corporation)
Predicting Cluster Tool Behavior with Slow Down
Factors
Robert Unbehaun and Oliver Rose (Dresden University of
Technology)
Abstract:
Cluster tools are representatives of a special kind of
tool where process times of jobs depend on the combination in which they are
processed together on the tool and hence, depending on the sequence in which
they are processed at a tool. To evaluate schedules of jobs to be processed at
such a tool an estimation method is needed since a detailed simulation takes
too long. In this paper, we present a method based on slow down factors which
produces promising results and gives hints for the development of intelligent
scheduling methods for this kind of tools.
An Analysis of Tool Capabilities in the
Photolithography Area of an Asic Fab
P. J. Byrne, Cathal Heavey,
and Kamil Erkan Kabak (University of Limerick)
Abstract:
Photolithography is generally regarded as the most
constraining element in semiconductor manufacturing. This is primarily
attributable to the high capital investment and extensive reentrant flows
throughout this section. Cycle time management in this area is crucial to
balance the trade off between tool utilization and cycle time. In a low
volume, high product mix fab the inclusion of tool capabilities, and their
status, can significantly affect tool utilization and overall cycle times. In
this paper a simulation model is developed to aid cycle time decision making
policies in the photolithography section of a low volume, high product mix
fab. The objective of the study is to determine the optimum course of action,
for varying levels of expected increased demand, while maintaining acceptable
cycle times and minimizing total capital spent in photolithography. The
actions reviewed include the increased use of capabilities where available,
followed by the purchase of new photolithography equipment.
Simulation Results and Formalism for Global-local
Scheduling in Semiconductor Manufacturing Facilities
Mickael
Bureau, Stephane Dauzere-Peres, and Claude Yugma (Ecoles des Mines de
Saint-Etienne) and Leon Vermarien and Jean-Bernard Maria (STMicroelectronics)
Abstract:
This article deals with an approach for managing
scheduling in semiconductor manufacturing facilities. The proposed approach
ensures consistency between global and local scheduling decisions, by ensuring
that global objectives are met through dynamic adaptation of the local
behavior. This approach is validated by simulation. After describing the
context and the framework of the approach, we introduce the formalism and
present first simulation results obtained on real data of the fab of
STMicroelectronics, Rousset. The experimental tests are promising since
substantial improvements are obtained on criteria such as cycle time, number
of completed lots, etc.
Wednesday 10:30:00 AM 12:00:00 PM
AMHS Modeling Approaches and
Distributed Simulation
Chair: Theresa Roeder (San Francisco State
University)
Hierarchical Distributed Simulation for 300mm Wafer
Fab
Sheng Xu and Leon F. McGinnis (Georgia Institute of Technology)
Abstract:
Distributed simulation promises benefits in large-scale
simulations, such as in high fidelity simulation of 300mm wafer fabs, although
these benefits have been hard to achieve in practice. This paper examines the
fundamentals of distributed simulation, and proposes a hierarchical approach
to distributed wafer fab simulation, which has the potential to achieve
significant reduction in model execution time.
Survey of Research in Modeling Conveyor-based
Automated Material
Dima Nazzal and Ahmed El-Nashar (University of
Central Florida)
Abstract:
Automated material handling systems (AMHS) play a
central role in modern wafer fabrication facilities (fabs). Typically, AMHS
used in wafer fabs are based on discrete vehicle-based overhead systems such
as overhead hoisted vehicles. Conveyor-based continuous flow trans-port (CFT)
implementations are starting to gain support with the expectations that CFT
systems will be capable of handling high-volume manufacturing transport
requirements. This paper discusses literature related to models of conveyor
systems in semiconductor fabs. A comprehensive overview of simulation-based
models is provided. We also identify and discuss specific research problems
and needs in the design and control of closed-loop conveyors. It is concluded
that new analytical and simulation models of conveyor systems need to be
developed to understand the behavior of such systems and bridge the gap
between theoretical research and industry problems.
Reusable Tool for 300mm Intrabay Amhs Modeling
and Simulation
Ahmed El-Nashar (University of Central Florida) and
Khaled S. El-Kilany (Arab Academy for Science and Technology)
Abstract:
The transition to 300mm wafer size introduced a lot of
new technologies to wafer fabrication facilities that mandated the presence of
intrabay automated material handling systems (AMHS) for moving wafer carriers
between the stockers and production tools within a bay. The design of intrabay
AMHS depends on the configuration and the mode of delivery. A generic reusable
tool is developed for modeling and simulation of the 300mm intrabay AMHS
different designs. The tool relies on a built-in database and a library
containing the different components of intrabay AMHS and the different
processing tools. The design of the generic tool guarantees its reusability
for building different models of bays with virtually any design. The tool
output includes a number of AMHS performance metrics that can be used
effectively in comparing different designs of an intrabay AMHS.
![]()