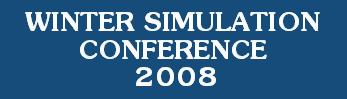 |
WSC 2008 Final Abstracts |
Manufacturing Applications Track
Monday 10:30:00 AM 12:00:00 PM
Input Data and Validation
Chair: Guodong Shao (National Institute of Standards and Technology)
A New Procedure Model for Verification and Validation
in Production and Logistics Simulation
Markus Rabe (Fraunhofer
IPK), Sven Spieckermann (SimPlan AG) and Sigrid Wenzel (Universitaet Kassel)
Abstract:
Verification & Validation of simulation models and
results has been strongly investigated in the context of defence applications.
Significantly less substantial work can be found for applications for
production and logistics, which is surprising when taking into account the
massive impact that wrong or inadequate simulation results can have on
strategic and investment-related decisions for large production and logistics
systems. The authors have, therefore, founded an expert group for this
specific topic in the year 2003, which has analysed the existing material and
then developed proposals for definitions, overviews on existing V&V
techniques, practical hints for the documentation of the procedural steps
within a simulation study, and a specific procedure model for V&V in the
context of simulation for production and logistics. The results of this
working group are available as a textbook, in German. This paper summarises
major results.
A Methodology for Input Data Management in
Discrete Event Simulation Projects
Anders Skoogh and Björn
Johansson (Chalmers University of Technology)
Abstract:
Discrete event simulation (DES) projects rely heavily
on high input data quality. Therefore, the input data management process is
very important and, thus, consumes an extensive amount of time. To secure
quality and increase rapidity in DES projects, there are well structured
methodologies to follow, but a detailed guideline for how to perform the
crucial process of handling input data, is missing. This paper presents such a
structured methodology, including description of 13 activities and their
internal connections. Having this kind of methodology available, our
hypothesis is that the structured way to work increases rapidity for input
data management and, consequently, also for entire DES projects. The
improvement is expected to be larger in companies with low or medium
experience in DES.
A Discrete Event Simulation Model for Reliability
Modeling of a Chemical Plant
Bikram Sharda and Scott Bury (The Dow
Chemical Company)
Abstract:
This paper discusses a discrete event simulation model
developed to identify and understand the impact of different failures on the
overall production capabilities in a chemical plant. The model will be used to
understand key equipment components that contribute towards maximum production
loss and to analyze the impact of a change policy on production losses. A
change policy can be classified in terms of new equipment installation or
increasing the stock level for the failure prone components. In this paper, we
present the approach used and some preliminary results obtained from available
data.
Monday 1:30:00 PM 3:00:00 PM
Balancing and Bottleneck Detection
Chair: Ander Skoogh (Chalmers University of
Technology)
A New Method for Bottleneck
Detection
Sankar Sengupta (Oakland University), Kanchan Das (East
Carolina University) and Robert VanTil (Oakland University)
Abstract:
This paper presents a new method to identify and rank
the bottlenecks in a manufacturing system. The proposed method is based on
performance related data that are easy to capture, offers low computational
burden and less prone to be in error due to its simplicity. The proposed
method analyzes inter-departure time from different machines to identify and
rank the bottlenecks. In a follow-up paper the authors plan to present a
method to allocate loss of production to different machines based on analysis
of inter-departure time. This paper also proposes a set of rules that may be
used to improve data integrity. The proposed method may be used to analyze
both steady state as well as non-steady state data and can be extended easily
to analysis of a job shop.
Metodology for Selecting the Best Suitable
Bottleneck Detection Method
Eliseu Lima and Leonardo Chwif (Escola
de Engenharia Maua) and Marcos Ribeiro Pereira Barretto (Universidade de São
Paulo)
Abstract:
Focusing on process constraints (or bottlenecks) is how
companies are improving productivity, decreasing response times. However, a
bottleneck is not easily detectable, especially when conventional bottleneck
methods are used. This work presents a method, based on simulation, to help
the selection of the bottleneck detection method to be applied to a given
situation. The methodology extends previous works on the subject, mainly those
by Roser, Nakano and Tanaka (2002) and Roser, Nakano and Tanaka (2003). The
proposed method was successfully applied to a real bottling process.
Mixed Model Assembly Line Balancing Problem with Fuzzy
Operation Times and Drifting Operations
Weida Xu and Tianyuan Xiao
(National CIMS Engineering Research Center)
Abstract:
Assembly line balancing problem (ALBP) means assigning
a series of task elements to uniform sequential stations under certain
restrictions. This paper considers a special type of assembly line balancing
problem with mixed models, fuzzy operation times and drifting operations,
which has the objective of minimizing the total work overload time. According
to chance constrained programming, a fuzzy alpha total work overload time
minimization model is built. Moreover, fuzzy simulation and genetic algorithm
are integrated to design a hybrid intelligent algorithm to solve the above
model. Finally, Extensive computational results are reported to demonstrate
the efficiency and effectiveness of the algorithm.
Monday 3:30:00 PM 5:00:00 PM
Standards and Model Building
Chair: Salla Lind (VTT, Technical Research Centre of Finland)
Automating the Development of Shipyard
Manufacturing Models
Gabriel A. Burnett, Daniel A. Finke, D.J.
Medeiros, and Mark T. Traband (The Pennsylvania State University)
Abstract:
Simulation results are often needed within a short time
frame, while the development of simulation models can be time consuming. We
develop a methodology to facilitate rapid generation of simulation models from
an enterprise database. Data is communicated between Product Lifecycle
Management (PLM) software and Flexsim using a standard Microsoft Excel format.
We have developed a custom Flexsim interface and software-specific model
generator that creates a discrete event simulation model from the PLM input
data. Preliminary results show that the methodology can reduce the cost of
simulation model generation while simultaneously improving the accuracy of
generated models. This work highlights the benefits of automatic model
generation techniques, describes a shipbuilding implementation of the
methodology, and provides direction for future work.
Representing Layout Information in the CMSD
Specification
Frank Riddick and Yung-Tsun Tina Lee (National
Institute of Standards and Technology)
Abstract:
Developing mechanisms for the efficient exchange of
information between simulations and other manufacturing tools is a critical
problem. For many areas of manufacturing, neither representations for the
information nor mechanisms for exchanging the information have been agreed
upon. Manufacturing plant layout is one such area. The Core Manufacturing
Simulation Data (CMSD) specification is being developed to address some of
these issues, through the definition of neutral representations for the “core”
manufacturing entities that need to be exchanged between simulations and other
applications, through the creation of a Unified Modeling Language information
model that defines the relationships between the core manufacturing entities,
and through the definition of eXtensible Modeling Language Schemas based on
the information model to facilitate the exchange of information that adheres
to the model. This paper describes an effort to extend the CMSD specification
to cover the definition and exchange of layout information.
Tuesday 8:30:00 AM 10:00:00 AM
Emulation
Chair: Matias Urenda
Moris (University of Skövde)
Emulation in Manufacturing Engineering
Processes
Hironori Hibino (JSPMI)
Abstract:
In our research, the manufacturing system emulation
technology is proposed as one of the frontloading methods in the manufacturing
system implementation phase. In this paper, the roles of the manufacturing
system emulation technology in manufacturing engineering processes are
summarized based on our analysis for the typical manufacturing engineering
processes. The manufacturing system emulation environment (MSEE) to implement
the manufacturing system emulation is proposed and developed. MSEE consists of
our developed manufacturing cell emulator, our developed soft-wiring system,
and the industrial network middleware which is one of the semi-standard
middlewares. The validation of our proposed environment was carried out
through a case study.
Architecture for Modeling, Simulation, and Execution
of PLC Based Manufacturing System
Devinder Thapa, S.C. Park, Gi-Nam
Wang, and C. M. Park (Ajou University) and Hee Han Kwan (Gyeongsang National
University)
Abstract:
In this paper, we propose an integrated architecture
for modeling, simulation, and execution of PLC (Programmable Logic Controller)
based manufacturing system. The main objective is to integrate the high level
modeling, simulation, and device level executable code generation. This
architecture can improve the fidelity between high level system model and
lower level PLC controlled devices. In this paper, we model the shop floor
controller system using DEVS (Discrete Event System Specification) formalism,
subsequently, simulate the model and generate SOP (sequence of operations). We
added two algorithms in conventional DEVS, the first algorithm makes an
interface between 3D graphic model and DEVS model, whereas, the second
algorithm generates SOP. As a result, the generated SOP can be mapped with PLC
I/O (Input/Output) address to generate an executable controller code. For the
purpose of further validation and implementation, the generated program can be
downloaded to software or hardware PLC.
Offline Commissioning of a PLC-Based Control System
Using Arena
Jeffrey S Smith and Younghol Cho (Auburn University)
Abstract:
In this paper, we address a generalized method of
mapping a control system simulation model to the PLC emulator being tested
using model variables and PLC tags under the offline commissioning
environment. For this research we created an example system similar to a high
speed packaging system described in a previous WSC paper. Implementation
experience using Rockwell Software applications is provided.
Tuesday 10:30:00 AM 12:00:00 PM
Maintenance
Chair: Sanjay Jain
(The George Washington University)
Optimized Maintenance Design for Manufacturing
Performance Improvement Using Simulation
Ahad Ali (Lawrence
Technological University), Xiaohui Chen (Chongqing University), Ziming Yang
(University of Michigan – Ann Arbor), Jay Lee (University of Cincinnati) and
Jun Ni (University of Michigan – Ann Arbor)
Abstract:
This research presents optimized maintenance design
using simulation to analyze the capability of auto part manufacturing
production system. The integration of simulation and optimization is used to
identify critical stations, an optimal system design and maintenance
scheduling schemes and evaluates their effects on the overall system
performance. Most emphasis is focused on the impact on system by individual
station reliability and the fluctuation of maintenance availability. The
proposed simulation and optimization for maintenance design is validated
through real-life application. This simulation modeling and optimization could
help for manufacturing performance improvement.
Simulation and Mathematical Programming for a
Multi-Objective Configuration Problem in a Hybrid Flow
Shop
Pierpaolo Caricato, Antonio Grieco, and Francesco Nucci
(University of Lecce, Dep. of Innovation Engineering)
Abstract:
This paper introduces an application of
simulation-based multi-objective optimization to solve a system configuration
problem in a hybrid flow shop system. The test case is provided by a firm that
manufactures mechanical parts for the automotive sector. We present an
architecture that uses both discrete-event simulation and mathematical
programming tools in order to solve the problem. The multiple-objective nature
of the problem is preserved throughout the proposed approach, using
Pareto-dominance concepts both to eliminate inefficient solutions within the
proposed solution algorithm and to provide the user with efficient solutions.
Mathematical programming is used to cull the required number of simulation
runs. Computational results obtained using a real-world case study are
reported. The proposed approach is benchmarked against a general purpose
simulation-optimization engine in order to prove its effectiveness.
A Comparative Study of Genetic Algorithm Components in
Simulation-Based Optimisation
Birkan Can (Enterprise Research
Centre, University of Limerick), Andreas Beham (Upper Austria University of
Applied Sciences) and Cathal Heavey (Enterprise Research Centre, University of
Limerick)
Abstract:
In this paper, we present a comparative study of
different stochastic components of genetic algorithms for simulation-based
optimisation of the buffer allocation problem. We explore the effects of
elements such as operators, fitness assignment strategies and elitism. Three
different recombination operators, incorporated with constraint handling
mechanisms such as repair and penalty functions, are examined. Under the shed
of the experiments, we incorporate problem specific knowledge to further
enhance the practicality of GA in decision making for buffer allocation
problem.
Tuesday 1:30:00 PM 3:00:00 PM
Automotive
Chair: Ed Williams
(Production Modeling Corporation)
Applying a Simulation-Based Tool to Productivity
Management in an Automotive-Parts Industry
Adrián Aguirre
(Industrial Engineering Department (FIQ-UNL)), Enrique Müller and Sebastián
Seffino (Industrial Engineering Department (FIQ-UNL)) and Carlos Alberto
Méndez (INTEC (UNL-CONICET))
Abstract:
This work presents the development and application of
an advanced modeling, simulation and optimization-based framework focused on
the production process of a basic element of a internal combustion engine
which is supplied by a leading factory in the Latin-American market. Lying on
the concepts of the process-interaction approach, the principal components
available in the discrete event simulation environment “SIMUL8” were used to
achieve the best representation of this complex manufacturing system.
Furthermore, advanced SIMUL8’s Visual Logic tools were utilized for modeling
specific design and operation features arising in the process under study. The
developed tool provides a support system for making operative, tactical and
strategic decisions, allowing the evaluation of possible scenarios ranging
from different operation schemes to potential alternatives of investment. The
principal aim of this work is to provide a systematic methodology to improve
the productive capacity management, enhancing the process profitability and
the degree of customer satisfaction.
Emergence of Simulations for Manufacturing Line
Designs in Japanese Automobile Manufacturing Plants
Minh Dang
Nguyen and Soemon Takakuwa (Nagoya University)
Abstract:
The aim of this research is to introduce the reader to
a new perspective on the framework for designing a manufacturing line project
in Japanese automobile manufacturing plants. All manufacturing aspects,
manual, automated and hybrid manufacturing lines are considered; however,
which line should be used for the factory is always under investigation within
the factory. Simulation studies that include resource utilization, line
productivity and manufacturing costs help to identify the most suitable
manufacturing line type within a factory. By utilizing simulation studies,
designers can make reliable decisions upon suitable manufacturing lines faster
than conventional methods based upon engineering experience. In order to
understand the framework of manufacturing line design, a project to design a
new automobile component manufacturing line was investigated in this study,
and the chosen manufacturing line was also checked by the manufacturing
activities in the factory.
Simulation Based Evaluation of the Workload
Control Concept for a Company of the Automobile Industry
Patrick
Kirchhof, Nicolas G. Meseth, and Thomas Witte (University of Osnabrueck)
Abstract:
This paper describes a simulation study conducted for a
company of the German automobile supply industry facing the need to improve
delivery reliability. The intention of the study was to evaluate whether
Workload Control (WLC) is applicable as production control policy for this
company and whether improvement can be expected. Therefore the regarded shop
floor was modeled being organized as a WLC production system. Both, the
structural and quantitative model components of the developed simulation model
are explained in depth. Furthermore it is shown how inherent parameters of the
WLC concept can be set using the simulation model in a practical environment.
As due date compliance is the primary concern of the company, the performance
of four simple priority dispatching rules is analyzed with regard to delivery
reliability. As a result it is shown that WLC is applicable in the given
situation and that performance enhancements can be
expected.
Tuesday 3:30:00 PM 5:00:00 PM
System Design 1
Chair:
Deogratias Kibira (National Institute of Standards and Technology)
A Proposal for Coordinator Control Recipe
in a Batch Process
Jose Francisco Briones de la Torre (Universidad
Politecnica de Aguascalientes) and Antonio Espuña Camarasa and Luis Puigjaner
Corbella (Universidad Politecnica de Cataluña)
Abstract:
In this work, we propose a coordinator control recipe
in the context of a batch process with the use of elements of petri nets and
some techniques associated with non linear control (e.g. the relative degree)
focused to explain the implications of use a hybrid dynamical models in terms
of problem control and its relation with on-line experimental measures and the
norm ISA S88.02
Clarifying Conwip Versus Push System Behavior Using
Simulation
Silvanus T. Enns and Paul Rogers (University of Calgary)
Abstract:
This research examines the performance of CONWIP versus
“push” workload control in a simple, balanced manufacturing flowline.
Analytical models and simulation experiments are used to evaluate the
tradeoffs between throughput and inventory performance. Tradeoff curves based
on inflating the inventory level for the CONWIP system and the arrival rate
for the “push” system are generated. As well, the variability of interarrival
and processing times are considered as experimental factors. Results show
that, contrary to what some previous studies have indicated, CONWIP efficiency
is not inherently superior to “push” system efficiency. Instead, the release
mechanism used for the “push” system has a significant impact on which system
will perform better. Utilization levels and processing time variability also
affect the relative performances.
Tradeoffs in Building a Generic Supply Chain
Simulation Capability
Sanjay Jain (The George Washington
University)
Abstract:
Building a simulation model for any large complex
system requires high expertise and effort. These requirements can be reduced
through building generic simulation capability that includes artifacts for
facilitating the development of the simulation model. The artifacts can have a
range of capabilities depending on the design goals for the simulation. This
paper focuses on issues to be considered in building a generic simulation
capability for supply chains. A number of approaches used in recent years for
building generic supply chain simulation capability are discussed. Such
approaches include data-driven simulators, interactive simulators, and
sub-models for supply chain components. Tradeoffs are identified that should
be considered in selecting an approach for building a generic supply chain
simulation capability.
Wednesday 8:30:00 AM 10:00:00 AM
System Design 2
Chair: Mark
Aufenange (University of Paderborn)
A Simulation Based System for Analysis and
Design of Production Control Systems
Corinne MacDonald and Eldon
Gunn (Dalhousie University)
Abstract:
We present aspects of a simulated based system for
analyzing and designing production control systems. The core of the system is
a simulation of a manufacturing system operating with the Production
Authorization Card system. The simulation model is fast and flexible, making
it attractive for generating large datasets for use in developing simulation
metamodels of expected performance for a wide variety of production
configurations. Details of the simulation system are provided, along with a
discussion of the issues to be considered when using it to design production
control systems.
The Use of Simulation for Process Improvement in
Metal Industry - Case Ht-lasertekniikka
Toni Petteri Ruohonen
(University of Jyväskylä)
Abstract:
Companies in the metal industry want to find solutions
for increasing the quality of service and productivity of the operation, but
it is not an easy task to do, especially if the company is large (has several
different production units) and in addition uses many different metal types as
material. This paper examines the centralization of special metal production
into a single unit instead of several units. The research method is simulation
and the main concentration is on finding out the effects and the possible
benefits of the centralization scenario. Two different simulation models are
constructed for the study. The results of the simulation runs showed that the
centralization would increase the utilization of a selected unit only 3,12 %
which means that it could be easily carried out. The results also indicated
that the centralization scheme could improve the operation significantly
(elimination of operational and logistics phases).
Iterative Use of Simulation and Scheduling
Methodologies to Improve Productivity
Karthik Krishna Vasudevan,
Edward John Williams, Ravi Lote, and Onur M. Ulgen (PMC)
Abstract:
Experienced and wise industrial engineering educators
and practitioners have long understood that industrial engineering is a
coherent discipline encompassing techniques that work best synergistically,
not a motley collection of specialized techniques each isolated in a separate
chimney. As an example of the synergies which industrial engineering can bring
to process improvement in a production environment, this case study presents
the integrated use of process simulation, production scheduling, and detailed
analysis of material-handling methods and their improvement. The study
undertook the identification and improvement of production and scheduling
policies to the benefit of a manufacturing process whose original throughput
capacity fell significantly short of high and increasing demand.
Wednesday 10:30:00 AM 12:00:00 PM
System Design 3
Chair: Toni
Ruohonen (University of Jyväskylä)
Using Simulation with Design for Six Sigma in
a Server Manufacturing Environment
Sreekanth Ramakrishnan
(Binghamton University, State University of New York), Christiana M Drayer
(IBM Corporation) and Pei-Fang Tsai and Krishnaswami Srihari (Binghamton
University, State University of New York)
Abstract:
This research presents an integrated simulation
modeling-Design For Six Sigma (DFSS) framework to study the design and process
issues in a server manufacturing environment. The server assembly process is
characterized by long cycle times, high fall-out rates and extremely complex
assembly operations. To ensure on-time customer delivery, these enterprises
adopt a make-to-plan and build-to-order philosophy. However, this model is
extremely complex, resulting in wastes and inefficiencies in the associated
processes. Lean and six sigma approaches have been successful in improving
performance by eliminating waste in the design and operational processes. In
this study, an integrated simulation modeling - DFSS framework is proposed to
(i) address effects of variation, (ii) assess interactions effects between
various sub-systems, and (iii) study proposed process (or design) changes,
while performing “what-if” analysis. This framework was then used to identify
opportunities for improving the operational and design issues in a server
manufacturing environment.
Simplification and Aggregation Strategies
Applied for Factory Analysis in Conceptual Phase Using
Simulation
Matías Urenda Moris, Amos H.C. Ng, and Jacob Svensson
(University of Skövde)
Abstract:
Despite that simulation possesses an establish
background and offers tremendous promise for designing and analyzing complex
production systems, manufacturing industry has been less successful in using
it as a decision support tool, especially in the conceptual phase of factory
design. This paper presents how simplification and aggregation strategies are
incorporated in a modeling, simulation and analysis tool, with the aim of
supporting decision making in conceptual phase. Conceptual modeling is guided
by a framework using an object library with generic drag and drop system
components and system control objects. Data inputs are simplified by the use
of Effective Process Time distributions and a novel aggregation method for
product mix cycle time differences. The out coming specification is through a
Web Service interface handle by modeling system architecture, automatically
generating a simulation model and analysis. Case studies confirm a
breakthrough in project time reduction without appreciable effects on the
model’s fidelity.
Simulation-Based Sustainable Manufacturing System
Design
Juhani Heilala, Saija Vatanen, Jari Montonen, and Hannele
Tonteri (VTT Technical Research Centre of Finland), Björn Johansson and Johan
Stahre (Chalmers University of Technology) and Salla Lind (VTT Technical
Research Centre of Finland)
Abstract:
Manufacturing simulation and digital engineering tools
and procedures have had a positive impact on the manufacturing industry.
However, to design a sustainable manufacturing system, a multitude of system
dimensions must be jointly optimized. This paper proposes an integrated
simulation tool helping to maximize production efficiency and balance
environmental constraints already in the system design phase. Lean
manufacturing, identification and elimination of waste and production losses,
and environmental considerations are all needed during development of a
sustainable manufacturing system. Engineers designing the manufacturing system
need decision support, otherwise sub-optimization is more likely to occur. We
present methods for calculating energy efficiency, CO2 emissions and other
environmental impacts integrated into factory simulation software.
![]()