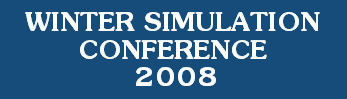 |
WSC 2008 Final Abstracts |
MASM - Operational Modeling and Simulation Track
Monday 10:30:00 AM 12:00:00 PM
Simulation-Based Decision-Making
Chair: Gerald Weigert (Dresden University of
Technology)
A Full-Factory Simulator as a Daily
Decision-Support Tool for 300mm Wafer Fabrication
Productivity
Sugato Bagchi (IBM T.J. Watson Research Center),
Ching-Hua Chen-Ritzo (IBM T. J. Watson Research Center) and Sameer T Shikalgar
and Michael Toner (IBM Systems and Technology Group)
Abstract:
We describe a discrete event simulator developed for
daily prediction of WIP position in an operational 300mm wafer fabrication
factory to support tactical decision-making. The simulator is distinctive in
that its intended prediction horizon is relatively short, on the order of a
few days, while its modeling scope is relatively large. The simulation
includes over 90% of the wafers being processed in the fab and all process,
measurement and testing tools. The model parameters are automatically updated
using statistical analyses performed on the historical event logs generated by
the factory. This paper describes the simulation model and the parameter
estimation methods. A key requirement to support daily and weekly
decision-making is good validation results of the simulation against actual
fab performance. Therefore, we also present validation results that compare
simulated production metrics against those obtained from the actual fab, for
fab-wide, process, tool and product specific metrics.
Coping with Typical Unpredictable Incidents in a
Logic Fab
Wolfgang Scholl (Infineon Technologies Dresden)
Abstract:
Within the last months the semiconductor plant of
Infineon in Dresden has converted to a pure manufacturer of logic products.
With it, premises for production control have changed to short and, first of
all, predictable cycle times. Typical for a logic fab, intelligent performance
monitoring and prediction methods have to be installed, coping scheduled and
unscheduled disturbances. Most important method is transient fab simulation,
giving a 3-months performance forecast based on actual line situation and
planned changes in toolset and product mix. This continuous forecast has to be
enriched with information to scheduled and unscheduled fab disturbances for
just in time initiation of countermeasures in case of foreseeable excursions,
e.g. changes in dispatching. In particular, breakdowns have to be analyzed
from historical data to find typical patterns, for probability of occurrence
and, especially, machine group specific behavior. This paper presents the
procedure on the basis of three examples.
Experimental Study on Variations of Wipload Control in
Semiconductor Wafer Fabrication Environment
Appa Iyer Sivakumar
(Singapore-MIT Alliance), Chao Qi (Huazhong University of Science and
Technology) and Andy Darwin (Singapore-MIT Alliance)
Abstract:
WIPLOAD Control has been proposed and evaluated as an
effective job release control methodology. This paper presents a further
simulation experimental study on two variations of WIPLOAD Control in
semiconductor wafer fab environment. The first variation mechanism is to
control separate WIPLOAD for each part type at a specified level under the
situation when the type of job going to be released next can be controlled.
The second variation is a mechanism with additional release control points
along the production line. The performance of the WIPLOAD variations are
compared with that of the original WIPLOAD Control and other existing release
methods including CONWIP and Constant release in semiconductor manufacturing
environment. The experimental results indicate that by breaking down the
control of overall fab WIPLOAD into controlling WIPLOAD level for each part
type, cycle time performance can be improved especially with respect to the
standard deviation of cycle time.
Monday 1:30:00 PM 3:00:00 PM
Factory Scheduling
Chair: Lars
Mönch (University of Hagen)
Simulation-Based and Solver-Based Optimization
Approaches for Batch Processes in Semiconductor
Manufacturing
Andreas Klemmt and Sven Horn (Electronics Packaging
Laboratory), Gerald Weigert (Dresden University of Technology) and Thomas
Hielscher (Qimonda)
Abstract:
Scheduling is one of the key factors for semiconductor
fabrication productivity. Objectives like lot cycle time and throughput must
be optimized to push the technological development and secure the existence on
the rapid growing global market. But especially in the frontend the
manufacturing process is dominated by cluster-tools and reentrance flows which
makes a production planning and optimization very hard. The workflow here is
mostly controlled only by dispatch rules. To get a further improvement in
manufacturing planning strategies, there is an increasing request of exact or
simulation-based solution methods for specified work centers or bottleneck
machine groups. One example of this is the semiconductor oven process. Here,
complex batch processes with a lot of restrictions have to be scheduled. A
reduction of cycle time in this section by optimized manufacturing strategies
has a great influence on all global optimization objectives. Two approaches
are investigated in this paper.
Bee Colony Optimization Algorithm with Big Valley
Landscape Exploitation for Job Shop Scheduling Problems
Li-Pei
Wong, Chi Yung Puan, and Malcolm Yoke Hean Low (Nanyang Technological
University) and Chin Soon Chong (Singapore Institute of Manufacturing
Technology)
Abstract:
Scheduling is a crucial activity in semiconductor
manufacturing industry. Effective scheduling in its operations leads to
improvement in the efficiency and utilization of its equipment. Job Shop
Scheduling is an NP-hard problem which is closely related to some of the
scheduling activities in this industry. This paper presents an improved Bee
Colony Optimization algorithm with Big Valley landscape exploitation as a
biologically inspired approach to solve the Job Shop Scheduling problem.
Experimental results comparing our proposed algorithm with Shifting Bottleneck
Heuristic, Tabu Search Algorithm and Bee Colony Algorithm with Neighborhood
Search on Taillard JSSP benchmark show that it is comparable to these
approaches.
Impact of Qualification Management on Scheduling in
Semiconductor Manufacturing
Carl Johnzén (STMicroelectronics),
Stéphane Dauzère-Pérès (Ecole des Mines de Saint-Etienne), Philippe
Vialletelle (STMicroelectronics) and Claude Yugma and Alexandre Derreumaux
(Ecole des Mines de Saint-Etienne)
Abstract:
A qualification management software that proposes
recipe qualifications on tools in toolsets for semiconductor manufacturing has
been developed. The qualification proposals are based on flexibility measures
that have been shown to model capacity allocation in semiconductor workshops.
In this paper, qualifications are used in order to see how increased
flexibility for the capacity allocation improve scheduling. For this a
scheduler simulator for the photolithography area has been used. Tests prove
that qualifications – if they are well managed – both enable the simulator to
achieve better scheduling and enable toolsets to be less sensitive to tool
breakdowns.
Monday 3:30:00 PM 5:00:00 PM
Queuing Models
Chair: Horst
Zisgen (IBM Deutschland)
A Queueing Network Based System to Model Capacity
and Cycle Time for Semiconductor Fabrication
Horst Zisgen and Ingo
Meents (IBM Deutschland), Benjamin R. Wheeler (IBM) and Thomas Hanschke
(Clausthal University of Technology)
Abstract:
In today's semiconductor business, wafer manufacturers
are facing continuous pressure to accurately predict cycle time and tool
utilization, gauge the impact of changes in capacity available and changes in
product mix, and determine action plans to improve operational performance.
Discrete Event Simulation (DES) is a widely used approach to perform such an
analysis. However, DES has some inherent shortcomings for these planning
tasks. Analytical models, like queueing networks, have much shorter response
times and additional advantages compared to DES. But due to the complexity of
semiconductor manufacturing systems (SMS) queueing models were not able to
model all the peculiarities of those. This paper provides an overview of the
IBM Enterprise Production planning and Optimization System (EPOS), a queueing
network based system, which closes this gap. EPOS has been in use in the 300mm
fabrication of IBM for more than 2 years and has turned out to be an
invaluable tool.
Characterizing the Departure Process from a Two
Server Markovian Queue: A Non-Renewal Approach
Guy L. Curry and
Natarajan Gautam (Texas A&M University)
Abstract:
For large queueing network analysis the general
computational approach is to utilize decomposition to facilitate computational
tractability. To accomplish this individual analysis the input and output
streams must be characte-rized. This usually is done via two-parameter
characterizations: the process mean and a variance measure (most commonly the
squared coefficient of variation SCV). In most approaches independent and
identically distributed (i.i.d.) approximations are used. For multiple input
streams and/or multiple (identical) servers, the assumptions of i.i.d. times
between arrivals and, similarly, i.i.d. times between departures are
particularly theoretically and computationally inaccurate. In this paper we
develop a generator for the background multidimensional continuous time Markov
chain associated with the inter-departure times for the associated
multi-stream and multi-server Markovian queues (where inter-arrival times and
service times are Coxian). This generator allows for the computation of the
moments of the departure process and the lag-k correlations between successive
k-separated departures.
Queueing Models for Single Machine Manufacturing Systems
with Interruptions
Kan Wu, Leon F. McGinnis, and Bert Zwart
(Georgia Tech)
Abstract:
Queueing theory is a well-known method for evaluating
the performance of manufacturing systems. When we want to analyze the
performance of a single machine, M/M/1 queues or approximations of G/G/1
queues often are considered a proper choice. However, due to the complex
nature of interruptions in manufacturing, the appropriate model should be
selected carefully. This paper proposes a systematic way to classify different
kinds of interruptions seen in a single machine system. Queueing models for
each category are proposed, and event classifications are compared from both
the SEMI E10 and queueing theory points of view.
Tuesday 8:30:00 AM 10:00:00 AM
Panel Discussion
Chair: John
Fowler (Arizona State University)
Modeling and Analysis of Semiconductor
Manufacturing in a Shrinking World: Challenges and
Successes
Chen-Fu Chien (TSMC), Stéphane Dauzère-Pérès (Ecole des
Mines de Saint-Etienne), Hans Ehm (Infineon Technologies AG), John W. Fowler
(Arizona State University), Zhibin Jiang (Shanghai Jiao Tong University),
Shekar Krishnaswamy (AMD), Lars Moench (University of Hagen) and Reha Uzsoy
(North Carolina State University)
Abstract:
A panel session on the role of modeling and analysis in
semiconductor manufacturing in a shrinking world is presented. Therefore, two
participants are from Asia, two from Europe, and two from US and there are two
panel organizers/moderators (Fowler and Mönch). One panelist from each
continent is from industry and one from academia. Only initial position
statements are included in the proceedings. However, these initial statements
form the basis for the panel discussion. The statements of the panelists from
industry relate to modeling and analysis problems found in their own
companies. The position statements of the panelists from academia describe the
role that modeling and analysis is expected to play in their current and
ongoing research in semiconductor manufacturing. Furthermore, their views on
the challenges and successes of modeling and analysis in a globalized world
are also included.
Tuesday 10:30:00 AM 12:00:00 PM
Modeling of Batching Tools
Chair: Reha Uzsoy (North Carolina State University)
Online Control of a Batch Processor with
Incompatible Job Families under Correlated Future Arrivals
John
Benedict Tajan (Singapore-MIT Alliance), Appa Iyer Sivakumar (Singapore-MIT
Alliance (Nanyang Technological University)) and Stanley Gershwin
(Singapore-MIT Alliance (Massachusetts Institute of Technology))
Abstract:
Oxidation and diffusion ovens in wafer fabrication are
batch processors; only jobs with identical job families can be processed
together. Initially, we use simulation to show that a heuristic based on Model
Predictive Control (MPC), with properly selected parameters, has up to 16.67%
lower mean cycle time than NACHM (a look-ahead method), under uncorrelated
arrivals. Controlling upstream processors according to the anticipated needs
of the batch processor may result in correlated families for successive
arrivals. Increasing correlation between arrivals almost always significantly
reduces the mean cycle time, for both policies. Furthermore, NACHM improves at
a faster rate than the MPC-based heuristic. Thus, when the correlation is high
(0.7) and the traffic intensity low (0.5), the MPC-based heuristic, has longer
mean cycle time (from 1.92% to 9.47%) than NACHM. Our results highlight the
benefits of constraining the upstream processor according to the anticipated
needs of the batch processor.
Time-Limited Next Arrival Heuristic for Batch
Processing and Setup Reduction in a Re-Entrant Environment
Stephen
Murray (Dublin City University), Steve Sievwright (Intel Ireland Ltd.) and
John Geraghty and Paul Young (Dublin City University)
Abstract:
This paper presents a new batch scheduling heuristic -
the Time-Limited Next Arrival heuristic for batch processing and setup
reduction (TLNA). This heuristic has been defined for a batch processing
machine group in a re-entrant manufacturing environment where setups are
sequence-dependent. When making the scheduling decision, TLNA takes into
account future arrivals based on a user-defined wait time. A series of
experiments is conducted on a discrete event simulation model to determine the
impact of this wait time. A total cost function is used to combine two
conflicting performance measures (total item queuing time and total machine
running time) into one. All TLNA wait time scenarios are compared to the Next
Arrival Control Heuristic for Multiple products and Multiple machines
(NACHMM). The experiments presented show that there is a wait time that
minimises the total operational cost. TLNA outperforms NACHMM with regard to
all performance measures except total queuing time.
Simulation Analysis of Semiconductor
Manufacturing with Small Lot Size and Batch Tool
Replacements
Kilian Schmidt (AMD Saxony LLC & Co. KG) and
Oliver Rose (Dresden University of Technology)
Abstract:
Long cycle times in semiconductor manufacuring
represent an increasing challenge for the industry and lead to a growing need
of break-through approaches to reduce it. Small lot sizes and the conversion
of batch processes to mini-batch or single-wafer processes are widely regarded
as a promising means for a step-wise cycle time reduction. However, there is
still a lack of comprehensive and meaningful studies. In this paper we present
first results of our modeling and simulation assessment. Our simulation
analysis shows that small lot size and the replacement of batch tools with
mini-batch or single wafer tools are beneficial but lot size reduction lacks
persuasive effectiveness if reduced by more than half.
Tuesday 1:30:00 PM 3:00:00 PM
Equipment Modeling
Chair: Julie
Christopher (IBM Microelectronics)
A Review of Scheduling Theory and Methods for
Semiconductor Manufacturing Cluster Tools
Tae-Eog Lee (KAIST)
Abstract:
Cluster tools, which combine several single-wafer
processing modules with wafer handling robots in a closed environment, have
been increasingly used for most wafer fabrication processes. We review tool
architectures, operational issues, and scheduling requirements. We then
explain recent progress in tool science and engineering for scheduling and
control of cluster tools.
Study of Optimal Load Lock Dedication for
Cluster Tools
Julie Christopher (IBM Microelectronics)
Abstract:
Cluster or chamber tools are often used in the
semiconductor industry. In a research environment, moving to smaller device
dimensions requires experimentation with new chamber types and materials to
overcome challenges with Moore’s Law. To make the most of expensive mainframes
and clean room floor space multiple chamber types can be placed on one
mainframe. Although this type of configuration can reduce cost while
evaluating new complex processes, the efficiency of the tool as a whole can be
drastically reduced. A major bottleneck within tools configured with multiple
process chambers can be the load locks. These load locks are the single wafer
entry point into the vacuum chamber. This paper will show the effect of load
lock dedication on a sample multi-process chamber tool.
Simulation Analysis of Cluster Tool Operations in
Wafer Fabrication
Amit Kumar Gupta (Birla Institute of Technology
and Science - Pilani, Hyderababd Campus), Peter Lendermann (D-SIMLAB
Technologies Pte Ltd) and Sivakumar Appa Iyer and John Priyadi (Nanyang
Technological University)
Abstract:
Cluster tools have been one of the proposed
alternatives to improve operations performance in semiconductor fabrication.
The benefits include high yield throughput, less contamination and less human
involvement. Perkinson et al. (1994, 1996) developed analytical models to
predict the minimum theoretical time required to complete the cycle in a
cluster tool. This paper addresses the verification of these analytical models
using simulation. Two simulation models were developed – one with simple
configuration and another one that incorporates parallel chambers. The
implementation of parallel chambers for the longest process in the cluster
tool is tested as the potential area of performance improvement.
Tuesday 3:30:00 PM 5:00:00 PM
AMHS Modeling and Simulation
Chair: Jens Zimmerman (University of Hagen)
An Analytical Model for Conveyor Based AMHS in
Semiconductor Wafer Fabs
Dima Nazzal (University of Central
Florida), Andrew Johnson (Texas A&M University), Hector J. Carlo
(University of Puerto-Rico-Mayagüez) and Jesus A. Jimenez (Texas State
University)
Abstract:
This paper proposes an analytical model useful in the
design of conveyor-based Automated Material Handling Systems (AMHS) to support
semiconductor manufacturing. The objective is to correctly estimate the
work-in-process on the conveyor and assess the system stability. The analysis
approach is based on a queuing model, but takes into account details of the
operation of the AMHS including turntables. A numerical example is provided to
demonstrate and validate the queuing model over a wide range of operating
scenarios. The results indicated that the analytical model estimates the
expected work-in-process on the conveyor with reasonable accuracy.
A Simulation Based Approach for Supporting
Automated Guided Vehicles (AGVs) Systems Design
Elisa Gebennini,
Sara Dallari, Andrea Grassi, Giuseppe Perrica, Cesare Fantuzzi, and Rita
Gamberini (Dipartimento di Scienze e Metodi dell’Ingegneria - University of
Modena and Reggio Emilia)
Abstract:
Automated Guided Vehicle (AGV) logistic handling
systems are widely adopted when high transportation capacity and quality of
service are the most important characteristics to reach. A large number of
mathematical approaches have been developed in years to address AGV systems
design and control. Nevertheless, proper performance estimations have to
consider the peculiar aspects of the real environment in which the AGV system
operates. A simple and effective approach to the stochastic features modelling
is the discrete event simulation of the real system. This paper presents a
conceptual approach that lead the analyst to set up consistent simulative
models to address AGV systems design and performance estimation when
applications in end-of-line logistics are considered.
Determining an Appropriate Number of Foups in
Semiconductor Wafer Fabrication Facilities
Jens Zimmermann and Lars
Moench (University of Hagen), Scott J Mason (University of Arkansas) and John
W. Fowler (Arizona State University)
Abstract:
In this paper, multiple orders per job type formation
and release strategies are described for semiconductor wafer fabrication
facilities (wafer fabs). Different orders are grouped into one job because
orders of an individual customer very often fill only a portion of a
Front-Opening Unified Pod (FOUP). A FOUP is assigned to each job and is used
to move the job throughout the wafer fab after the job formation. We determine
an appropriate number of FOUPs for a given order release rate that will yield
acceptable values for on-time delivery performance, cycle time, and throughput
via discrete event simulation.
Wednesday 8:30:00 AM 10:00:00 AM
Simulation Applications
Chair: Stéphane Dauzère-Pérès (Ecole des Mines de Saint-Etienne)
Decision Making and Forecasting with Respect to
Risk: A Simulation Study for a Setup-Problem
Martin Romauch
(Infineon Technologies), Christian Almeder (University of Vienna) and Walter
Laure and Georg Seidel (Infineon Technologies)
Abstract:
In this paper, the impact of timing a setup operation
on the work-in-process and cycle time is investigated. Using a small example
of an reentrant production system, it is shown that there is a tradeoff
between reducing the average work-in-process inventory and guaranteeing a
smooth operation of the system. Furthermore it is shown, that an early setup
may lead to an increased variance of the cycle time, but regarding the number
of lots with an extreme excess of cycle time the timing decision has only a
minor influence.
An Experimental Study of an Iterative
Simulation-Optimization Algorithm for Production Planning
D. Fatih
Irdem, N. Baris Kacar, and Reha Uzsoy (North Carolina State University)
Abstract:
It is well known from queueing and simulation models
that cycle times in capacitated production systems increase nonlinearly with
resource utilization, which poses considerable difficulty for the conventional
linear programming (LP) models used for this purpose. Hung and Leachman (1996)
propose a highly intuitive iterative approach where a detailed simulation
model of the production facility is used to estimate flow time parameters used
in an LP model. We examine the convergence characteristics of this method
under different experimental conditions, and conclude that it is hard to
determine precisely when the method converges.
Analysis of Multiple Process Flows in an Asic Fab
with a Detailed Photolithography Area Model
Kamil Erkan Kabak and
Cathal Heavey (University of Limerick) and Vincent Corbett (Analog Devices)
Abstract:
ASIC fabs are characterized by multiple process flows.
This is mainly due to the highly diversified product portfolios within such
fabs. In this study, we first examined the cycle time for individual process
flows in a medium volume ASIC fab. We compared these process flows in terms of
overall cycle time and using a cycle time index. Secondly, focusing on
photolithography we developed a simulation model that employs cycle time data
to analyze the impacts of process flow diversity. Thirdly, we used this model
to examine the impact on cycle time of changing the volumes of wafer starts on
different process flows. The detailed results of simulation experiments along
with the concluding remarks are given at the end of the study.
Wednesday 10:30:00 AM 12:00:00 PM
Modeling Approaches and Optimization
Formulations
Chair: Chen-Fu Chien (National Tsing Hua University)
An Optimization Framework for Waferfab Performance
Enhancement
Boon Ping Gan (D-SIMLAB Technologies)
Abstract:
A typical wafer fab requires numerous decisions for
daily operations. Even small decisions on system configurations may have
significant impact on the overall fab performance. One of the most critical
performance measure is cycle time, where just one day of reduction could
represent significant cost savings. In this paper we describe an automated
simulation-based optimization method to improve fab configurations. We
illustrated our method through a case study that involves optimization of
multiple decision variables in a wafer fab. The objective of the optimization
is to reduce the cycle time. We show the potentials of such an optimization
through achieving an improvement of 15% in cycle time for a furnace toolset.
An Indirect Workforce (Re)allocation Model for
Semiconductor Manufacturing
Chen-Fu Chien (National Tsing Hua
University), Wen-Chih Chen (National Chiao Tung University) and Shao-Chung Hsu
(National Tsing Hua University)
Abstract:
Semiconductor industry is a capital intensive and
knowledge intensive industry, in which human resource management and human
capital enhancement is increasingly important. To maintain competitive human
resource, it is critical to develop a decision framework for headcount
planning and workforce allocation for indirect labors. This study aims to
develop a model for allocating indirect workforce among semiconductor
fabrication facilities to meet expected outputs and labor productivity
improvement. Workforce allocation and reallocation based on the overall
corporate workforce level is essential so that the shortage or exceed
workforce will be balanced among different production sites. The key to
achieve this purpose is the proper understanding of real requirements of each
production site according to its corresponding tasks assigned. Non-parametric
activity analysis approach is used for the workforce requirement estimation
given delegated tasks. The estimation is based on the best performance from
the past with adjustments reflecting the expected productivity growth.
Multi-Product Lot Merging/Splitting Algorithms for a
Semiconductor Wafer Fabrication
June-Young Bang, Jae-Hun Kang,
Bong-Kyun Kim, and Yeong-Dae Kim (KAIST)
Abstract:
This paper focuses on a lot merging/splitting problem
in a semiconductor wafer fabrication facility. In the fab, two or more lots
can be merged into a single lot if routes and all the processing conditions of
the lots are the same for a number of subsequent operations, and the merged
lot is split into the original lots at the point where the routes or
processing conditions become different. We suggest lot merging/splitting
algorithms to reduce the total tardiness of orders and the cycle times of the
lots. The suggested algorithms are evaluated through a series of simulation
experiments and the result shows that the algorithms work better than a method
used in a real fab.
![]()