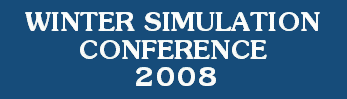 |
WSC 2008 Final Abstracts |
MASM - Supply Chain Management and Fab Economics
Track
Monday 10:30:00 AM 12:00:00 PM
Fab Economics
Chair: Kristin
Rust (Advanced Micro Devices)
Economic Efficiency Analysis of Wafer Fabrication
Facilities
Wen-Chih Chen (National Chiao Tung University) and
Chen-Fu Chien and Ming-Hsuan Chou (National Tsing Hua University)
Abstract:
Semiconductor industry is competitive, in which
efficiently utilizing resources to provide products and services is essential
for maintaining competitive advantages. Knowing whether the resource is
properly utilized is the foundation for future improvements and/or decision
making. This study aims to propose an economic efficiency study on fabrication
operations. We develop a two-stage overall efficiency model, which clearly
defines and explains the "real" performance of fab production operations and
the non-production issues. The model thus provides an overall performance
index while considering different aspects. A single performance index can used
to evaluate and rank the performance for period review. Furthermore, according
to a real case, an ex post relative efficiency analysis is conducted and the
initial results are reported. The case study can help providing diagnosis for
inefficient production facilities and identifying best practices of efficient
production units.
Using Little's Law to Estimate Cycle Time and
Cost
Kristin Rust (Advanced Micro Devices)
Abstract:
Well designed models can provide timely answers and
summarize understanding of complex systems. Simple use cases can illustrate
the applicability and inferences possible with even the most general models.
This paper uses Little’s Law to demonstrate the prediction of fab operating
conditions and associated cost implications.
Pricing Decision and Lead Time Setting in a Duopoly
Semiconductor Industry
I-Hsuan Hong, Hsi-Mei Hsu, Yi-Mu Wu, and
Chun-Shao Yeh (National Chiao Tung University)
Abstract:
Pricing and lead time setting are two important
decisions in semiconductor foundry industries. This research considers the
competition of a duopoly market consisting of two make-to-order firms in
semiconductor foundry industries and presents a model to determine the
equilibrium price and lead time of these two competing firms where each firm
maximizes its own revenue and is subject to its own constraints in a duopoly
market. In the model, customer mean demand rates of two competing firms are
assumed as functions of committed lead times and prices provided by these two
firms and the market. Furthermore, this paper utilizes a simulated procedure
to verify the equilibrium price and lead time obtained by the analytical model
presented in this paper.
Monday 1:30:00 PM 3:00:00 PM
Modeling Approaches in SCM
Chair:
Yi-Nung Yang (Chung Yuan Christian University)
Linear Inflation Rules for the Random Yield Production
Control Problem with Uncertain Demand: Analysis and
Computations
Woonghee Tim Huh (Columbia University) and Mahesh
Nagarajan (University of British Columbia)
Abstract:
Since the dawn of wafer fabrication and the production
of microelectronic parts a fundamental characteristic of this environment has
been uncertainty in production yields and in demand for product. The impact of
the uncertainty is so prevalent that even deterministic models in practice
have incorporated some allowance for uncertainty through features such as date
effective yields, moving average capacity, etc. In this paper, we propose a
simple heuristic approach for the inventory control problem with stochastic
demand and multiplicative random yield. Our heuristic tries to find the best
candidate within a class of policies which are referred to in the literature
as the linear inflation rule (LIR) policies. Our approach is computationally
fast, easy to implement and intuitive to understand. Moreover, we find that in
a significant number of instances our heuristic performs better than several
other well-known heuristics that are available in the literature.
A Contract of Purchase Commitments on Shared Yields
as a Risk-Sharing Mechanism among Fabless-Foundry
Partnership
Yi-Nung Yang (Chung Yuan Christian University) and
Shi-Chung Chang (National Taiwan University)
Abstract:
This paper develops a simple cooperative-game model for
an alliance with a design house and a foundry in a semiconductor supply chain.
In particular, we attempt to investigate an emerging observed type of
contracts among fabless-foundry partnership. It is termed the purchase
commitments on shared yields contract. We emphasize the risk-sharing aspect on
the contract by explicit modeling risk into the fabless and foundry's
objective functions. It is shown that the optimal share of yields depends on
two parties' expectations on prices of the products, risk-aversion, and scales
of production. The optimal share is not directly related to the both firms'
marginal cost of production. That is, this contract is a cost-invariant
contract. A Nash bargaining solution for the wholesale price under this
contract between fabless and foundry is also proposed.
Monday 3:30:00 PM 5:00:00 PM
Planning Methods
Chair: Ken
Fordyce (IBM)
Priority Mix Planning for Cycle Time-Differentiated
Semiconductor Manufacturing Services
Shi-Chung Chang, Shin-Shyu Su,
and Ke-Ju Chen (National Taiwan University)
Abstract:
Semiconductor fabs often offer manufacturing service of
multiple priorities in terms of cycle time-based X-factor targets (XFTs) and
fab production must be planned accordingly. This paper studies a priority mix
planning (PMP) problem that determines the wafer release rates of individual
priorities to maximize fab profit subject to XFT and capacity constraints. It
is formulated as a nonlinear programming problem, where the constraints
integrate an extended M/G/m:PR queue approximation with contribution
theory-based network for modeling how X-factors of individual priorities are
affected by priority mix and fab capacity utilization. It is then demonstrated
over a realistic fab example that PMP problem can be solved for effectively
planning priority mix and machine tool capacity utilization to provide
cycle-time differentiated manufacturing services.
Solving Volume and Capacity Planning Problems in
Semiconductor Manufacturing: A Computational Study
Christoph Habla
and Lars Moench (University of Hagen)
Abstract:
In this paper, we suggest a linear programming
formulation that allows for solving volume and capacity planning problems in
semiconductor manufacturing systems. We assume a general product structure
that includes commodities, custom products, finished products between these
two extreme classes, and several types of unfinished products. Computational
experiments with respect to the required level of detail of bottleneck
modeling are performed. Furthermore, we investigate the sensitivity of the
model with respect to noisy demand data. It turns out that the number of
modeled bottleneck is not crucial and that our approach can treat noisy demand
data appropriately.
The Ongoing Challenge – An Accurate Assessment of
Supply Linked to Demand to Create an Enterprise-Wide End to End Detailed
Central Supply Chain Plan
Ken Fordyce, John Milne, Alfred Degbotse,
Robert Orzell, Robert Rice, and Chi-Tai Wang (IBM)
Abstract:
Organizations can be viewed as an ongoing sequence of
loosely coupled decisions where current and future assets are matched with
current and future demand across the demand-supply network at different levels
of granularity ranging from a placing a lot on a tool to an aggregate capacity
plan across a five year horizon. Since the early 1990s detailed enterprise
wide central planning has become a key member of this “decision suite.”
Despite its importance, most organizations execute central planning with
“limited levels of accuracy or intelligence.” Early in the evolution of
“central planning engines” IBM determined that “extended accuracy” was an
important component of supply chain efficiency and customer satisfaction and
made a substantial investment to develop a central planning engine which could
handle the scope (complexity) and scale (size) of large organizations. This
presentation covers the value from this investment and the technical details
of combining heuristics and optimization.
Tuesday 8:30:00 AM 10:00:00 AM
Panel Discussion - See MASM Operational
Modeling and Simulation
Chair: John Fowler (Arizona State
University)
Tuesday 10:30:00 AM 12:00:00 PM
Scheduling Applications
Chair:
Tae-Eog Lee (KAIST)
Simulation Based Planning and Scheduling System for
TFT-LCD Fab
Bum C. Park and Eui S. Park (Samsung Electronics Co.
Ltd.), Byoung K. Choi (KAIST), Byung H. Kim (VMS Solutions Co. Ltd.) and Jin
H. Lee (KAIST)
Abstract:
In a typical LCD factory, a large number of product
types are produced concurrently, 24 hours a day and 365 days a year, and there
exist various constraints and re-entrant flows in the manufacturing processes.
As a result, efficient planning and scheduling of LCD production is a big
challenge. Presented in this paper is a simulation-based DPS (daily planning
& scheduling) system that was developed by the authors and is being used
in a modern LCD Fab in Korea. Also presented in the paper are a business
architecture of LCD production management, internal structure of the DPS
system, and Fab scheduling logic. The DPS system was installed at a large-size
LCD Fab in 2006, and the system has been successfully used for two years
leading to a considerable increase in on-time production of LCD panels and a
sharp decrease in turn-around time.
Technology That Upsets the Social Order – A
Paradigm Shift in Assigning Lots to Tools in Wafer Fabricator - The Transition
from Rules to Optimization
Richard Burda (IBM), Robert Bixby and
Vincent Gosselin (ILOG) and Ken Fordyce (IBM)
Abstract:
Historically the dominant decision technology to make
dispatch decisions was “rules” which involves the following basic
computational mechanisms: merge, select, sort, and if/then/else in a decision
tree. Although rules do a reasonable job they fundamentally lack a robust
ability to: (a) look across time, (b) look across tools at a tool set, (c)
create an anticipated sequence of events at a tool set over some time horizon,
(d) establish a formal metric and (f) search alternatives. However, standard
wisdom was the rapid pace of change and short time interval between dispatch
decisions precluded the use of optimization to build dispatch applications.
Although this barrier was legitimate in the 1980s and most of the 1990s based
on limitations in hardware and software (algorithms); the real barrier today
is cultural; not technical. From 2004-2007, IBM and ILOG jointly worked to
deploy the ILOG optimization product FPO to key tools sets in IBM’s 300mm fab
resulting in substantial improvements in performance and significantly reduced
overhead to adapt to changing circumstances. This paper will cover the
fundamentals of the paradigm shift.
Scheduling a Multi-Chip Package Assembly Line with
Reentrant Processes and Unrelated Parallel Machines
Sang-Jin Lee
and Tae-Eog Lee (KAIST)
Abstract:
A multi-chip package(MCP) consists of several chip
modules in a single package. We consider a scheduling problem for assembling
MCPs. In order to assemble anMCP, a lot should repeat assembly process stages
such as die attach and wire bonding as many as the number of chips to be
assembled. The two key process stages have many parallel machines of various
types. A machine processes different types of MCP lots with significant setup
times. We therefore should limit the number of setups significantly while not
sacrificing the on-time delivery performance much. We propose scheduling
strategies of appropriately allocating the machine capacity to products and
lots depending on the production progress of products and lots. We report
experimental performances of the proposed methods.
Tuesday 1:30:00 PM 3:00:00 PM
Simulation Applications in SCM
Chair: Robert Wright (International Sematech Manufacturing Initiative)
Framework for Execution Level Capacity
Allocation Decisions for Assembly – Test Facilities Using Integrated
Optimization - Simulation Models
Shrikant Jarugumilli and Mengying
Fu (Arizona State University), Naiping Keng and Chad DeJong (Intel
Corporation) and Ronald Askin and John Fowler (Arizona State University)
Abstract:
We present a framework for capacity allocation
decisions for Assembly-Test (A-T) facilities that is comprised of an
optimization model and a simulation model. The optimization and simulation
models are used iteratively until a feasible and profitable capacity plan is
generated. The models communicate using an automated feedback loop and at each
iteration the model parameters are adjusted. We describe the role of the
optimization model, the simulation model and the feedback loop. Once the
capacity plan is generated, it is passed down to the shop-floor for
implementation. Hence, decision makers can develop accurate and more
profitable execution level capacity plans using the integrated model which
utilizes both optimization and simulation models. In this paper, we focus on
the optimization model for capacity planning for the entire A-T facility at
the individual equipment (resource) level for a two-week planning period and
briefly discuss the simulation and the adjustment model.
Managing WIP and Cycle Time with the Help of Loop
Control
Steffen Kalisch, Robert Ringel, and Joerg Weigang (AMD
Saxony LLC & Co. KG)
Abstract:
As an adaptation of the CONWIP concept, AMD has
developed a heuristic approach to control the WIP in its wafer fabrication
facilities (fabs). The so called “Loop Control” concept helps to utilize the
installed equipment in an efficient way and reduces the overall cycle time.
Two dynamic constraints (the WIP-Limit and the THP-Limit) are defined to limit
the WIP (work in progress) per photo layer and to tackle high WIP situations
at individual operations inside a photo layer. Loop Control has been evaluated
with help of a fab simulation study prior to implementation in the fab
dispatching system. Since its development three years ago, this system
operates successfully in the AMD Dresden fabs.
High Speed Semiconductor Fab Simulation for Large,
Medium and Small Lot Sizes
Peter C Bosch (Highpoint Software
Systems, LLC) and Robert L. Wright (International SEMATECH Manufacturing
Initiative)
Abstract:
This paper describes an analysis performed to assess
the fidelity, scalability, and performance of the Sage® Fab Advisor™
semiconductor fab simulation engine executing two years of fab operations
across a range of lot sizes. We describe the demand and fab operations models
used, as well as the tools and methodology used in conducting the analysis.
Our results were validated against a well-known model running on a well-known
toolset, showing performance to be very competitive with that model. Further,
we show that our engine’s performance, running this model, scales almost
linearly from 25 wafer lot sizes down to single wafer lot sizes. That is,
simulation time increases roughly linearly with respect to the number of lots
being processed.
![]()